Making your own drums can be a fun and rewarding project. You don’t need to be an expert to get started.
Drums have been used in music for centuries. They come in many shapes and sizes. While buying a drum is easy, making one yourself adds a personal touch. This guide will help you understand the basics of drum-making. From choosing the right materials to assembling your drum, each step is simple to follow.
Whether you want a traditional drum or something unique, creating your own drum can be a fulfilling experience. Dive in to discover how you can craft your own musical instrument with ease.
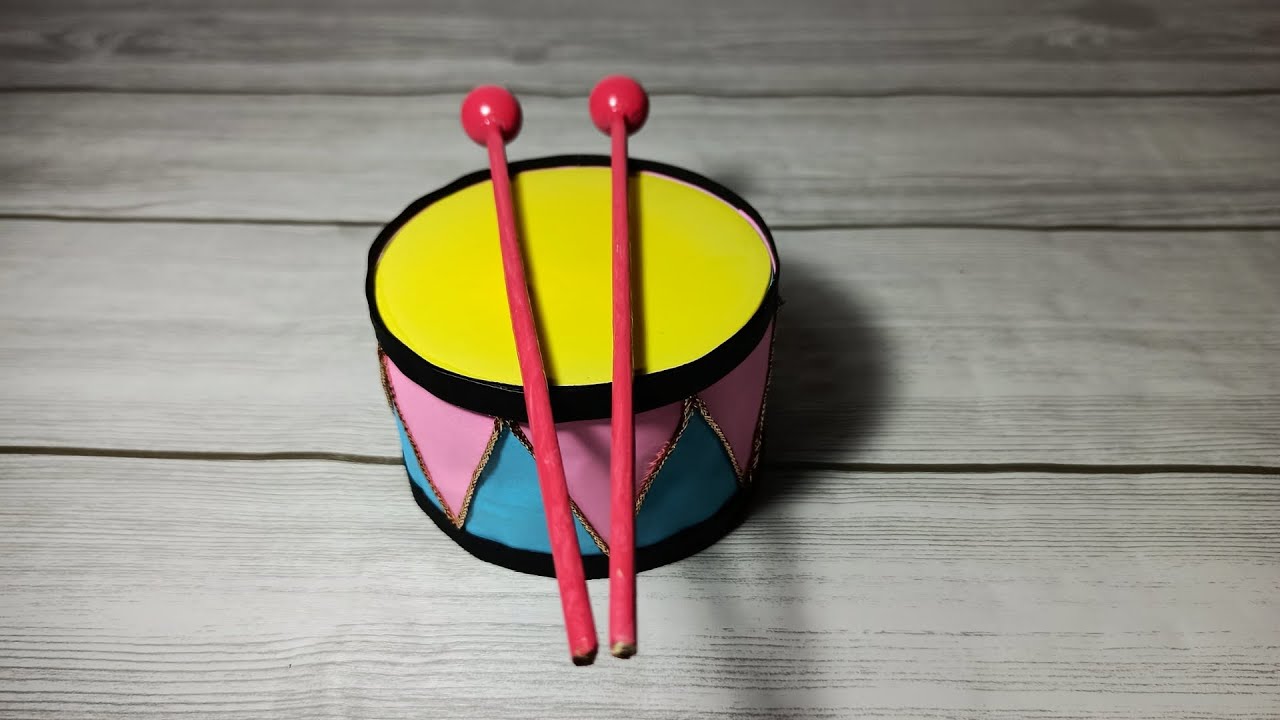
Credit: www.youtube.com
Materials Needed
Creating your own drum can be a rewarding experience. The first step is to gather the right materials. The materials you select will affect the drum’s quality and sound. In this section, we will explore the essential materials you need.
Wood Selection
The type of wood you choose is critical. Popular choices include maple, birch, and mahogany. Maple offers a balanced sound with good resonance. Birch gives a bright tone with a sharp attack. Mahogany provides a warm, rich sound.
Select wood that is free of knots and defects. This ensures the strength and durability of the drum shell.
Drum Skins
Drum skins are another important factor. Traditional drums use animal hides, like goat or cow. Synthetic skins are more common today. They are durable and consistent. Choose a skin that matches the drum’s size and desired sound.
Hardware And Tools
You will need various hardware and tools. Lugs and tension rods keep the drum skin tight. Hoops hold the skin in place. A drum key helps with tuning. You also need a saw, drill, and sandpaper for shaping and smoothing the wood.
Proper tools ensure a professional finish and sound quality. Invest in good quality tools for the best results.
Choosing Drum Type
Choosing the right drum type is essential. It shapes the sound and feel of your drum kit. Different drums serve unique purposes. Understanding each type helps you make informed decisions. Let’s dive into some common drum types.
Snare Drum
The snare drum is central to any drum kit. It produces sharp, staccato sounds. Its distinct sound comes from the wires, called snares, stretched across the bottom. Snare drums are versatile. They fit in various music styles, from rock to jazz. Consider the size and material. These factors affect the tone and volume.
Bass Drum
The bass drum is the heartbeat of your kit. It produces low, booming sounds. It is played with a foot pedal. This drum sets the rhythm and pace. Bass drums come in different sizes. Larger drums produce deeper tones. Smaller ones are punchier. Choose based on your music style and space.
Tom-toms
Tom-toms add color and texture to your drumming. They come in various sizes. Each size produces a different pitch. Tom-toms are mounted on stands or the bass drum. They are used in fills and solos. Choose a mix of sizes for a versatile sound. Experiment with placement for the best setup.
Creating The Shell
Creating the drum shell is an essential step in drum making. The shell must be sturdy and resonate well. This process involves cutting, shaping, and sanding the wood to achieve the desired sound quality.
Cutting The Wood
First, select the right type of wood. Maple, birch, and mahogany are popular choices. Each type has unique sound qualities. Measure the wood to the desired size using a tape measure. Use a saw to cut the wood into strips. Ensure each strip is of uniform thickness. This helps in creating a balanced sound.
Wood Type | Sound Quality |
---|---|
Maple | Warm and bright |
Birch | Sharp and punchy |
Mahogany | Rich and deep |
Shaping The Shell
Next, bend the strips into a circular shape. Use a mold to guide the shape. Apply a wood adhesive to the edges. Clamp the strips together tightly. Let the adhesive dry completely. This ensures the shell holds its shape.
- Bend the wood strips
- Apply wood adhesive
- Clamp and let dry
Sanding And Smoothing
After shaping, sand the shell to a smooth finish. Use different grits of sandpaper. Start with a coarse grit to remove rough edges. Gradually move to a finer grit. This creates a smooth, even surface. Ensure no rough spots remain. This step is crucial for a professional finish.
- Start with coarse grit sandpaper
- Progress to finer grits
- Check for smoothness
With a smooth shell, the drum is ready for the next steps. This careful attention to detail ensures the drum sounds great.
Applying Finishes
Once you have constructed your drum shell, it’s time to apply finishes. This process enhances the drum’s look and protects the wood. You can choose from various finishes. Each finish type offers different benefits and looks. Let’s explore the steps to achieve a professional finish.
Staining The Wood
Staining the wood adds color and highlights the grain patterns. Follow these steps:
- Prepare the surface: Sand the drum shell smoothly.
- Choose a stain: Select a color that matches your preference.
- Apply the stain: Use a cloth to rub the stain onto the wood.
- Wipe excess stain: Remove any excess with a clean cloth.
- Let it dry: Allow the stain to dry completely.
Applying Lacquer
Applying lacquer gives the drum a shiny finish and protects the wood. Follow these steps:
- Choose a lacquer: Water-based or oil-based options are available.
- Apply the first coat: Use a brush or spray to apply a thin layer.
- Sand the surface: Lightly sand with fine-grit sandpaper once dry.
- Apply additional coats: Repeat the process for 2-3 coats.
- Let it cure: Allow the lacquer to cure for several days.
Polishing
Polishing gives the drum a smooth, glossy finish. Follow these steps:
- Choose a polish: Use a wood polish or a car wax.
- Apply the polish: Rub the polish in circular motions.
- Buff the surface: Use a clean cloth to buff the drum to a shine.
- Inspect for spots: Check for any missed spots and repeat if needed.
By following these steps, your drum will look professional and be protected from damage. Applying finishes is a crucial part of drum-making. It not only improves appearance but also ensures longevity. Enjoy your beautifully finished drum!
Attaching Drum Skins
Attaching drum skins is a critical step in making drums. It affects sound quality and playability. This guide will help you through the process.
Selecting The Skin
Choosing the right drum skin is crucial. Natural skins offer a warm tone. Synthetic skins are more durable and consistent. Consider the music style you play.
Tensioning The Skin
Proper tensioning ensures the drum sounds good. Place the skin over the drum shell. Use a tensioning device or lugs to tighten it. Make sure the tension is even across the surface.
Tuning The Drum
Tuning the drum brings out the best sound. Tap the drum near each lug. Adjust the tension until the pitch is consistent. Repeat until satisfied with the sound.
Installing Hardware
Installing hardware on your drum is an essential step in the drum-making process. Proper installation ensures that your drum sounds great and is durable. This section will guide you through mounting the lugs, attaching the hoops, and adding the snare. Follow these steps carefully to achieve the best results.
Mounting The Lugs
First, gather the lugs and screws. Lugs hold the drumheads in place and allow tuning. Align the lugs evenly around the drum shell.
- Mark the lug positions using a pencil.
- Drill holes at the marked spots.
- Insert screws through the lugs and into the shell.
- Tighten the screws with a screwdriver.
Ensure all lugs are securely fastened. This will prevent issues during tuning.
Attaching The Hoops
Next, attach the hoops to the drum. Hoops keep the drumhead tensioned and help produce a clear sound. Place the drumhead on the drum shell.
- Position the hoop over the drumhead.
- Align the hoop with the lugs.
- Insert tension rods through the hoop and into the lugs.
- Turn the tension rods to tighten the hoop.
Tighten the rods evenly in a crisscross pattern. This ensures even tension across the drumhead.
Adding The Snare
Finally, add the snare to your drum. Snares are wires that create the drum’s distinctive “snap” sound. Attach the snare to the bottom hoop.
- Place the snare wires on the bottom drumhead.
- Attach the snare straps or cords to the snare throw-off.
- Secure the other end to the butt plate.
- Adjust the tension using the throw-off mechanism.
Test the snare to ensure it creates the desired sound. Adjust if necessary.
By carefully installing the hardware, your drum will be well-built and sound great. Follow these steps to ensure each part is securely attached.
Final Assembly
The final assembly of your drum kit is an exciting step. It’s where all your hard work comes together. This process requires patience and attention to detail. Let’s break it down into manageable steps.
Assembling The Drum Kit
Start by setting up the bass drum. Attach the legs and ensure they are stable. Next, place the toms on their stands. Adjust the height to your comfort. Finally, add the snare drum. Position it within easy reach.
Use a table to keep track of your setup:
Drum | Position | Notes |
---|---|---|
Bass Drum | Center | Ensure stability |
Toms | Above Bass Drum | Adjust height |
Snare Drum | Front and Center | Easy reach |
Positioning The Drums
Proper positioning is key to comfort and playability. Sit on your drum throne. Place the bass drum so your foot rests naturally on the pedal. Position the snare drum between your knees. Adjust the toms for easy reach. Ensure you can move your arms freely.
- Check the bass drum placement.
- Adjust the snare drum height.
- Align the toms for easy access.
Securing The Setup
Once positioned, secure each drum. Tighten the screws on the stands. Ensure the bass drum legs are locked. Check the snare drum stand for stability. Make sure nothing wobbles. Stability is crucial for a smooth performance.
Here are some key points to remember:
- Tighten all screws firmly.
- Ensure no parts are loose.
- Double-check stability before playing.

Credit: www.steampoweredfamily.com
Testing And Adjusting
After crafting your drum, testing and adjusting are crucial steps. This ensures your drum produces the best sound. Even small changes can make a big difference. Let’s explore how to fine-tune your drum for optimal performance.
Sound Check
Start with a basic sound check. Tap the drum lightly. Listen to the tone. If the sound is dull, the drumhead might be too loose. If it sounds too sharp, the drumhead might be too tight. Adjust the tension accordingly. Play different areas of the drum to check for consistency. Each part should produce a similar tone.
Fine-tuning
Fine-tuning your drum involves detailed adjustments. Use a drum key to tighten or loosen the drumhead. Make small changes and test the sound. Repeat until you reach the desired tone. If one side sounds different, adjust it slightly. Balance is key. The drum should sound harmonious.
Maintenance Tips
Regular maintenance keeps your drum in top shape. Check the tension of the drumhead frequently. Keep the drum clean. Wipe it down with a soft cloth. Store your drum in a cool, dry place. Avoid extreme temperatures. They can damage the drumhead. Inspect the hardware. Ensure all parts are secure. Replace worn-out parts promptly.

Credit: www.steampoweredfamily.com
Can I Use Techniques from Pentatonix to Make My Own Drums?
If you’re looking to enhance your percussion skills, you can explore ways to discover pentatonix’s unique drum sounds. By analyzing their techniques and experimenting with vocal layering and beatboxing, you can create your own rhythmic patterns that capture their distinct style, transforming everyday objects into your personal drum kit.
Frequently Asked Questions
What Materials Are Needed To Make Drums?
To make drums, you need a drum shell, drumheads, tension rods, and a drum hoop. Additionally, you’ll need drumsticks, a drum key, and hardware for assembly.
How Do You Choose Drum Shells?
Choose drum shells based on the type of wood, size, and thickness. Different woods produce different sounds. Popular choices include maple, birch, and mahogany.
What Tools Are Required To Assemble Drums?
You need a drum key, screwdriver, and a tuning wrench. These tools help assemble and tune the drumheads properly.
How Do You Tune Drumheads?
Tighten the tension rods evenly around the drumhead using a drum key. Tap the drumhead near each rod and adjust until the pitch is consistent.
Conclusion
Making drums is a fun and rewarding project. You now have the steps to create your own. Gather your materials. Follow the process carefully. Enjoy the creative journey. Your homemade drums will sound great. Share your new skill with friends.
Keep practicing and experimenting. Happy drumming!
{ “@context”: “https://schema.org”, “@type”: “FAQPage”, “mainEntity”: [ { “@type”: “Question”, “name”: “What materials are needed to make drums?”, “acceptedAnswer”: { “@type”: “Answer”, “text”: “To make drums, you need a drum shell, drumheads, tension rods, and a drum hoop. Additionally, you’ll need drumsticks, a drum key, and hardware for assembly.” } } , { “@type”: “Question”, “name”: “How do you choose drum shells?”, “acceptedAnswer”: { “@type”: “Answer”, “text”: “Choose drum shells based on the type of wood, size, and thickness. Different woods produce different sounds. Popular choices include maple, birch, and mahogany.” } } , { “@type”: “Question”, “name”: “What tools are required to assemble drums?”, “acceptedAnswer”: { “@type”: “Answer”, “text”: “You need a drum key, screwdriver, and a tuning wrench. These tools help assemble and tune the drumheads properly.” } } , { “@type”: “Question”, “name”: “How do you tune drumheads?”, “acceptedAnswer”: { “@type”: “Answer”, “text”: “Tighten the tension rods evenly around the drumhead using a drum key. Tap the drumhead near each rod and adjust until the pitch is consistent.” } } ] }