Yes, you can 3D print a saxophone. It’s a fascinating blend of technology and music.
Imagine playing a saxophone made from a 3D printer. This concept is not only possible but also increasingly popular. 3D printing allows musicians to create custom instruments. It’s a game-changer for those seeking unique sounds and designs. The technology behind this process is both complex and intriguing.
It involves layer-by-layer creation of the saxophone using special materials. This method opens new possibilities in the world of music. It enables more people to access and create their own instruments. Whether you are a musician or a tech enthusiast, 3D printing a saxophone can be an exciting project. Let’s dive into how this remarkable process works and what it means for the future of music.
Introduction To 3d Printing
3D printing has transformed the way we create objects. This technology allows you to make physical items from digital files. With 3D printing, you can create almost anything, including musical instruments like a saxophone.
Basics Of 3d Printing
3D printing, also known as additive manufacturing, builds objects layer by layer. It starts with a digital model, usually created with computer-aided design (CAD) software. The printer reads the digital file and lays down material, layer by layer, to form the object.
This process can use various materials. The most common are plastics, but metals, ceramics, and even food can be printed.
Here are the basic steps:
- Create a 3D model using CAD software.
- Convert the model into a format the printer can understand, like STL.
- Set up the printer with the required material.
- Start the print job and wait for your object to be built.
Popular 3d Printing Technologies
Several 3D printing technologies are available, each with unique advantages. Here are some of the most popular:
Technology | Description | Common Uses |
---|---|---|
Fused Deposition Modeling (FDM) | Builds objects by melting and extruding plastic filament. | Prototyping, hobby projects, simple models. |
Stereolithography (SLA) | Uses a laser to cure liquid resin into solid parts. | High-detail models, dental molds, jewelry. |
Selective Laser Sintering (SLS) | Fuses powder particles with a laser to form solid objects. | Functional parts, complex geometries, durable goods. |
Each technology has specific strengths. FDM is affordable and widely available. SLA offers high detail and smooth finishes. SLS is great for strong and complex parts.
Understanding these basics helps you decide which 3D printing method suits your project best. Creating a saxophone using 3D printing is possible. It combines art and technology in exciting ways.
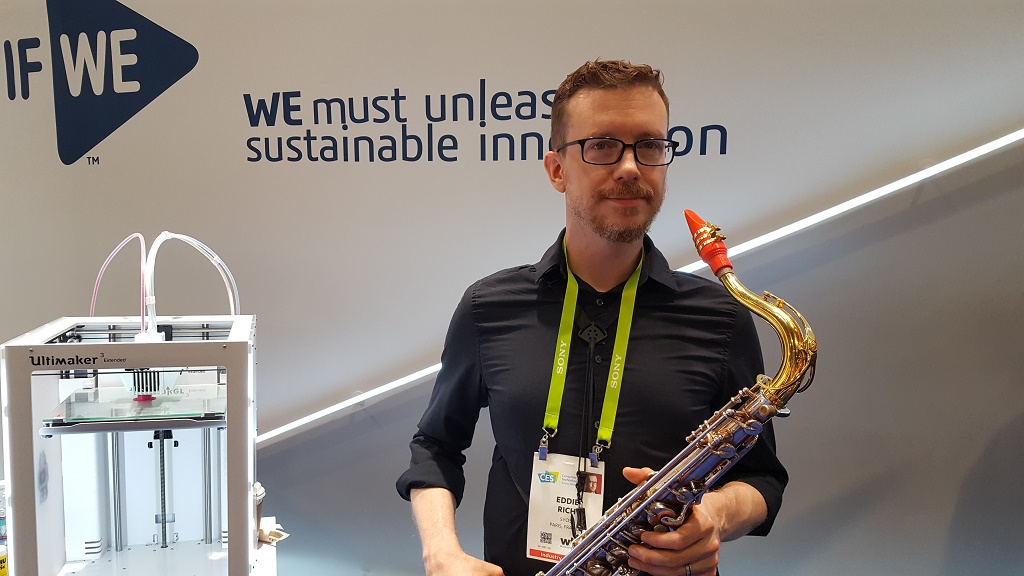
Credit: 3dprint.com
3d Printing In Music
3D printing is changing many fields, including music. Musicians and instrument makers use 3D printing to create unique instruments. This new technology allows for creativity and innovation. One interesting question is whether you can 3D print a saxophone. Let’s explore how 3D printing is used in music.
Applications In Instrument Making
3D printing has many uses in instrument making. Here are some applications:
- Prototyping: Create prototypes of new instrument designs quickly.
- Customization: Make custom parts for instruments to fit the musician’s needs.
- Repairs: Produce replacement parts for broken instruments.
- New Instruments: Design and print entirely new instruments.
For example, 3D printing can create unique shapes and designs for instruments. This opens up many possibilities for instrument makers. It allows for more experimentation and creativity.
Benefits And Challenges
3D printing in music has several benefits and challenges. Let’s look at some of them:
Benefits | Challenges |
---|---|
Fast Prototyping | Material Limitations |
Cost-Effective | Durability Issues |
Customization | Precision Concerns |
Innovation | Sound Quality |
Fast prototyping allows for quick testing of new designs. Cost-effective production means lower costs for creating instruments. Customization offers tailored solutions for musicians. Innovation brings new and unique designs to the music world.
On the other hand, there are challenges. Material limitations may affect the sound quality. Durability issues mean 3D printed parts may not last as long. Precision concerns can impact the accuracy of the instrument. Lastly, achieving the desired sound quality can be difficult with 3D printed materials.
Designing A 3d Printed Saxophone
Designing a 3D printed saxophone is a fascinating and complex task. It combines modern technology with traditional musical craftsmanship. Many enthusiasts and musicians are now exploring the potential of 3D printing. They aim to create functional and unique musical instruments. The process involves several steps, starting from the design phase.
Software Tools For Design
To design a 3D printed saxophone, you need the right software tools. CAD (Computer-Aided Design) software is essential. Tinkercad, Fusion 360, and SolidWorks are popular choices. These tools help you create detailed and precise models. They allow you to visualize the final product. You can modify the design easily before printing.
Tinkercad is user-friendly and great for beginners. Fusion 360 offers advanced features for more complex designs. SolidWorks is powerful and used by professionals. Choose the software that matches your skill level and project needs. Learning these tools can take some time. But, the results are worth the effort.
Technical Specifications
When designing a 3D printed saxophone, pay attention to technical specifications. The size and shape of the saxophone are crucial. You must ensure it is ergonomically designed. The instrument should be comfortable to hold and play. The dimensions must be accurate to produce the correct sound.
Material selection is also important. PLA and ABS are common 3D printing materials. PLA is easier to print but less durable. ABS is stronger but requires a heated bed. Each material affects the sound quality differently. Experiment with different materials to find the best one for your saxophone.
Wall thickness and infill density are other key factors. Thicker walls provide more strength but add weight. Infill density affects the instrument’s resonance. A higher density gives a richer sound but increases print time. Balance these factors to achieve a playable and durable saxophone.
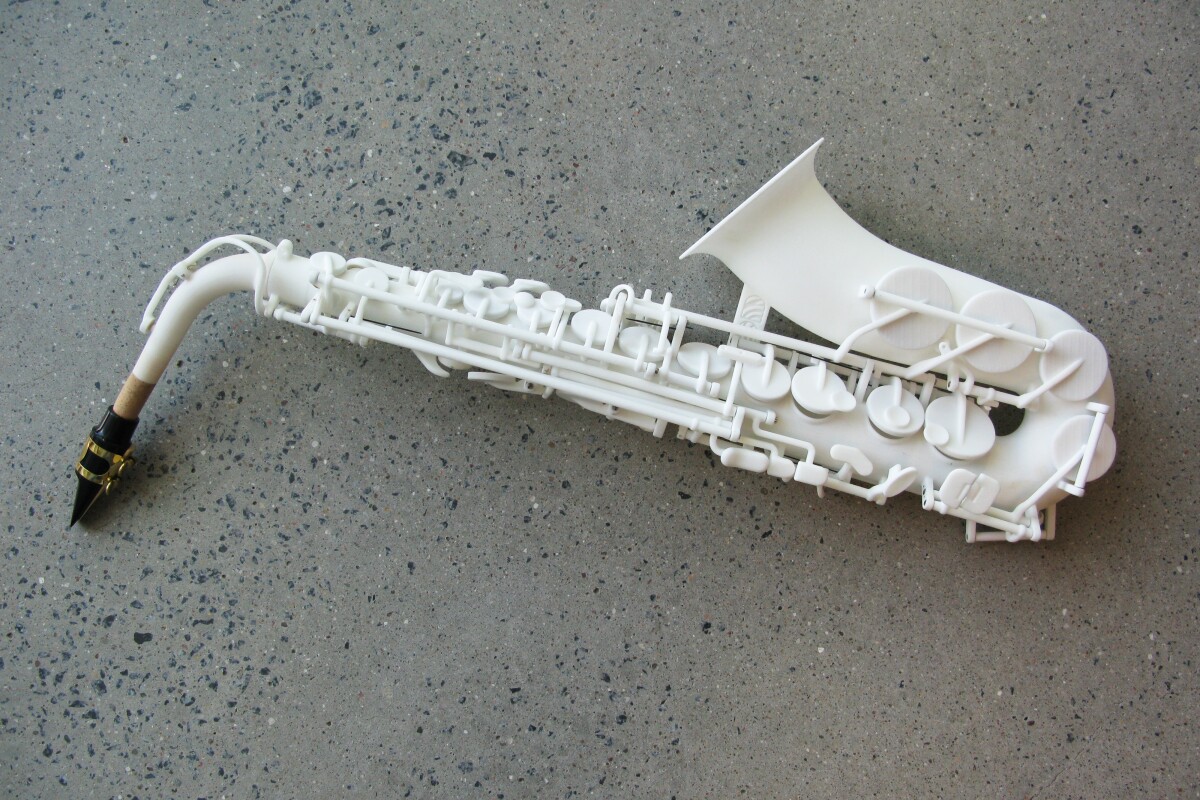
Credit: newatlas.com
Materials For 3d Printing Saxophones
Yes, you can 3D print a saxophone using materials like PLA, ABS, and resin. These materials help create lightweight, durable instruments. Enjoy creating custom designs and unique sounds with 3D printing technology.
3D printing a saxophone is an exciting idea. The choice of material plays a crucial role. The material used affects the saxophone’s sound, durability, and appearance.Commonly Used Materials
PLA (Polylactic Acid) is a popular choice. It’s easy to use and affordable. ABS (Acrylonitrile Butadiene Styrene) is another option. It’s more durable than PLA. PETG (Polyethylene Terephthalate Glycol) offers a good balance. It combines the ease of PLA and durability of ABS.Material Properties And Sound Quality
PLA is rigid and produces a bright sound. It’s lightweight, making it easier to handle. ABS is tougher and more flexible. This material gives a warmer tone. PETG is strong and flexible. It provides a balanced sound quality. Each material brings unique qualities to the saxophone. Choose the material that best fits your needs. “`Step-by-step Printing Process
3D printing a saxophone is a fascinating process. This section will guide you through the step-by-step printing process. You will learn how to prepare your printer and create a saxophone layer by layer. Follow these steps for a successful print.
Preparing The Printer
To start, make sure your printer is ready. This involves setting up the machine and preparing the materials.
- Clean the Printer: Ensure the printer is clean and free of debris.
- Check the Filament: Use a high-quality filament suitable for musical instruments.
- Calibrate the Printer: Properly calibrate the printer to ensure accuracy.
Once the printer is prepared, load the design file. This file should be a detailed 3D model of a saxophone. You can find these files online or create one using design software.
Layer-by-layer Printing
The printing process involves creating the saxophone layer by layer. This method ensures each part is precise and strong.
- Start the Print: Initiate the printing process on your 3D printer.
- Monitor the Layers: Keep an eye on the printer as it builds each layer.
- Adjust Settings: Make adjustments if the printer encounters issues.
Each layer is crucial. The printer will build the saxophone from the bottom up. This process can take several hours, so be patient. Ensure the print bed is stable and level throughout the process.
After the printing is complete, you will have a fully formed saxophone. You may need to do some post-processing, like sanding or painting, to finish the instrument.
Post-processing Techniques
3D printing a saxophone is exciting, but it’s just the start. Post-processing techniques are vital to achieve a smooth and functional instrument. These steps enhance the appearance and playability of your 3D printed saxophone.
Sanding And Smoothing
Sanding is a critical step. It removes rough edges and layer lines. Start with a coarse grit sandpaper, like 100 grit. Gradually move to finer grits, such as 200 and 400 grit. This ensures a smooth finish.
Use a sanding block for flat surfaces. For curved areas, sanding sponges or flexible sandpaper work well. Wet sanding can be useful too. It reduces dust and gives a finer finish. After sanding, the saxophone will be much smoother.
Assembling Parts
Most 3D printed saxophones come in multiple parts. Assembling them properly is crucial. First, ensure all parts are clean and smooth. Check if they fit together seamlessly.
Use a strong adhesive suitable for plastics. Apply it carefully to the joining surfaces. Press the parts together firmly. Hold them in place until the adhesive sets. Clamps or rubber bands can help keep parts aligned.
After the glue dries, inspect the joints. Sand any excess glue for a clean look. Now, your 3D printed saxophone is ready for final touches.
Step | Details |
---|---|
1. Sanding | Start with coarse grit, finish with fine grit |
2. Cleaning | Ensure all parts are smooth and dust-free |
3. Assembling | Use strong adhesive, align parts carefully |
4. Final Touches | Inspect joints, sand excess glue |
Testing And Tuning
Testing and tuning a 3D-printed saxophone is a crucial step. The process ensures the instrument sounds right and plays well. Just printing the saxophone is not enough. Careful adjustments and tests are needed.
Initial Sound Tests
After printing, the saxophone needs initial sound tests. Start by assembling the instrument. Ensure all parts fit correctly. Once assembled, play a few notes. Listen carefully to the sound produced.
Check for any unexpected noises. Also, make sure the notes are clear. If the sound is off, there may be issues. The problem could be with the 3D print or the assembly.
Adjusting For Optimal Performance
Adjustments are often needed for optimal performance. Start with the mouthpiece. It must fit well and be correctly positioned. Small changes can have a big impact.
Next, check the keys and pads. They should cover the tone holes completely. If not, air may leak, affecting the sound. Make necessary adjustments to ensure a proper seal.
Finally, test the instrument again. Play a range of notes. Listen for any improvements or remaining issues. Repeat adjustments as needed until the saxophone plays well.
Case Studies And Examples
Yes, you can 3D print a saxophone. Various case studies and examples show successful projects. These printed saxophones can produce music, though sound quality may differ from traditional ones.
In the fascinating world of 3D printing, creating musical instruments stands out. Especially intriguing is the possibility of 3D printing a saxophone. Let’s explore some case studies and examples to understand the progress and challenges in this unique endeavor.Successful 3d Printed Saxophones
Several innovators have successfully 3D printed saxophones. One notable example is Olaf Diegel, a professor at Lund University. He created a fully functional saxophone using a 3D printer. This saxophone was made of nylon material. It had the same key layout as a traditional saxophone. Musicians who played it noted its surprising sound quality. Another example is the Printone project by a team of researchers. They focused on creating wind instruments, including saxophones, with 3D printers. They aimed to make instruments accessible and customizable. The project showed that 3D printing could replicate complex shapes required for a saxophone.Lessons Learned
Several lessons emerged from these case studies. First, material choice is crucial. Nylon has been effective, but researchers are exploring other materials. The goal is to find a material that balances durability and sound quality. Second, the design process requires precision. Small changes can affect the sound. 3D printing allows for intricate designs, but careful planning is necessary. Researchers must consider the acoustics of each part. Lastly, accessibility remains a significant advantage. 3D printing makes it easier for individuals to create custom instruments. This opens new possibilities for musicians and hobbyists alike.Future Of 3d Printed Instruments
The future of 3D printed instruments is exciting. This technology is changing how we make and play music. 3D printing allows for unique designs. It also makes instruments more affordable. One interesting example is the 3D printed saxophone. This new method of making instruments could change the music industry.
Innovations On The Horizon
3D printing opens many possibilities. New materials and techniques are being developed. These innovations will improve sound quality. They will also make instruments more durable.
For example, some companies are experimenting with composite materials. These materials combine the best properties of different substances. This can create saxophones that are both lightweight and strong.
Another innovation is customization. Musicians can now design instruments to fit their needs. They can adjust the size, shape, and even the sound. This level of customization was not possible before.
Impact On The Music Industry
3D printing could have a big impact on the music industry. It can make instruments more affordable. This will make music accessible to more people. Schools and community centers could benefit from cheaper instruments.
It also allows for rapid prototyping. Musicians and designers can quickly test new ideas. This speeds up the development of new instruments.
Here is a simple table to show some potential benefits:
Benefit | Explanation |
---|---|
Affordability | Lower cost of production |
Customization | Instruments tailored to individual needs |
Rapid Prototyping | Quick testing of new designs |
Overall, 3D printing has the potential to change the music industry. It offers new opportunities for creativity and innovation.
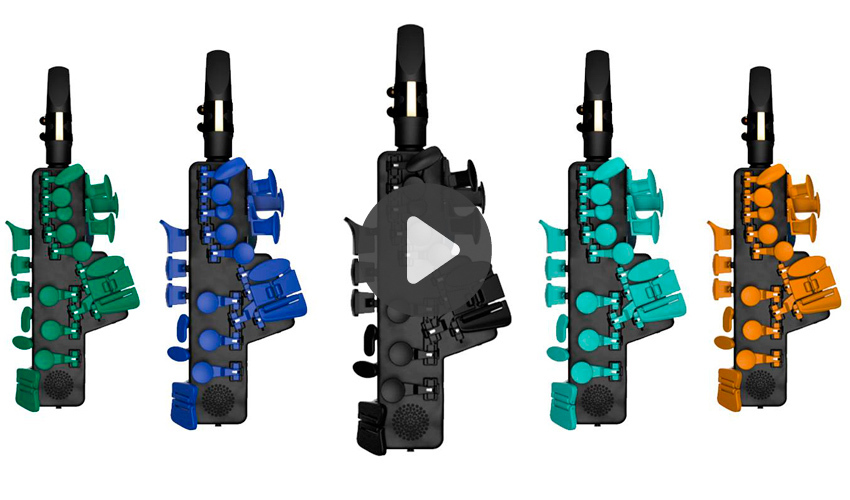
Credit: www.3dnatives.com
Frequently Asked Questions
Can You 3d Print A Saxophone?
Yes, you can 3D print a saxophone. Advances in 3D printing technology allow the creation of functional musical instruments. However, achieving the desired sound quality might require experimentation with materials and designs.
What Materials Are Used For 3d Printing Saxophones?
Common materials for 3D printing saxophones include PLA, ABS, and resin. Each material has different properties affecting the instrument’s durability and sound quality. Experimenting with various materials can help achieve the best results.
How Long Does It Take To 3d Print A Saxophone?
The printing time varies based on the saxophone’s size and complexity. Typically, it can take from several hours to a few days. Post-processing and assembly also add to the total time.
Is A 3d-printed Saxophone Playable?
A 3D-printed saxophone can be playable, but it may not match traditional saxophones’ sound quality. Proper design and material choice are crucial for achieving a playable instrument. Tuning and adjustments might be necessary for optimal performance.
Conclusion
3D printing a saxophone is possible and fascinating. It combines music and technology. While not perfect, it offers exciting potential. With improving technology, results will get better. Musicians and hobbyists can explore new possibilities. It’s an innovative way to create instruments.
Try it if you love music and tech. The future holds endless opportunities for 3D printed instruments.
{ “@context”: “https://schema.org”, “@type”: “FAQPage”, “mainEntity”: [ { “@type”: “Question”, “name”: “Can you 3D print a saxophone?”, “acceptedAnswer”: { “@type”: “Answer”, “text”: “Yes, you can 3D print a saxophone. Advances in 3D printing technology allow the creation of functional musical instruments. However, achieving the desired sound quality might require experimentation with materials and designs.” } } , { “@type”: “Question”, “name”: “What materials are used for 3D printing saxophones?”, “acceptedAnswer”: { “@type”: “Answer”, “text”: “Common materials for 3D printing saxophones include PLA, ABS, and resin. Each material has different properties affecting the instrument’s durability and sound quality. Experimenting with various materials can help achieve the best results.” } } , { “@type”: “Question”, “name”: “How long does it take to 3D print a saxophone?”, “acceptedAnswer”: { “@type”: “Answer”, “text”: “The printing time varies based on the saxophone’s size and complexity. Typically, it can take from several hours to a few days. Post-processing and assembly also add to the total time.” } } , { “@type”: “Question”, “name”: “Is a 3D-printed saxophone playable?”, “acceptedAnswer”: { “@type”: “Answer”, “text”: “A 3D-printed saxophone can be playable, but it may not match traditional saxophones’ sound quality. Proper design and material choice are crucial for achieving a playable instrument. Tuning and adjustments might be necessary for optimal performance.” } } ] }