Classical guitars are crafted by shaping wooden pieces into a body, neck, and headstock. Artisans then add strings and detailed tuning mechanisms to finalize the instrument.
Delving into the artistry behind classical guitars unveils a fusion of time-honored methods and meticulous craftsmanship. Expert luthiers carefully select quality woods such as spruce, cedar, and rosewood, each contributing to the instrument’s tone and aesthetic. Crafting a classical guitar starts with precision work on the soundboard, bracing patterns, and the hollow body’s curves, all of which affect the resonance and sound projection.
The neck, usually made of mahogany or cedar, is joined to the body, and a fretted fingerboard is attached. With fine inlays and varnishing, these instruments are not only sonic delights but also visual works of art. This meticulous process, often done entirely by hand, ensures each classical guitar is a testament to acoustic excellence and aesthetic beauty.

Credit: www.yamaha.com
Introduction To Classical Guitars
The classical guitar, with its rich harmonies and intimate character, embodies a tradition of musical craftsmanship that spans centuries. Often referred to as the Spanish guitar, its gentle nylon strings resonate with a warmth favored by concert performers and enthusiasts alike. This segment of our blog delves into the meticulous process behind creating classical guitars, a craft mastered by luthiers who ensure each chord strikes the perfect blend between history and melody.
Distinctive Features Of Classical Guitars
Classical guitars stand out due to several distinctive features that shape their unique sound and playability:
- Nylon Strings: Unlike acoustic guitars that use steel strings, classical guitars utilize nylon strings, which produce a softer, mellower sound.
- Wider Neck: The significant width of the neck allows for comfortable finger placement, essential for executing complex classical compositions.
- Smaller Body: A more compact body size enhances the clarity and balance of tones, requiring a delicate touch from the guitarist.
- Distinctive Headstock: Often featuring a slotted design, it contributes to the signature aesthetic and functionality of the classical guitar.
Historical Evolution Of Guitar-making Techniques
The art of guitar-making, or lutherie, has witnessed profound changes over the centuries:
- The early instruments from the Renaissance period laid the groundwork with simple, yet effective construction techniques.
- Baroque-era enhancements introduced ornate details and refined the shape of the guitar, leading to improved sound quality.
- The iconic Spanish luthiers of the 19th century, like Antonio Torres, revolutionized the build, achieving the classical guitar’s golden standard.
- Modern times saw the introductions of industrial processes alongside traditional handcrafting methods, sustaining the production of classical guitars while ensuring the nuanced qualities of each instrument.
Raw Materials And Components
The heart and soul of a classical guitar start with the quality and selection of its raw materials and components. These foundational elements define not only the appearance and durability but also the sound and overall performance of the instrument. Skilled luthiers choose from a variety of woods and other materials with precision and care, ensuring each classical guitar resonates with its own unique character.
Types Of Wood Used In Construction
The choice of wood used in a classical guitar is critical for both its tonal quality and structural integrity. Here’s a look at the woods commonly used:
- Spruce – Known for its clear, crisp sound; often used for the guitar’s top.
- Cedar – Offers a warmer tone; also commonly used for the top.
- Mahogany – Provides a rich, resonant quality, typically used for the back and sides.
- Rosewood – Favored for its complex overtones, used for back, sides, and fretboards.
- Maple – Seen less frequently but appreciated for its bright sound characteristics.
Selection Process For Materials
For a luthier, selecting the appropriate materials is a meticulous process. Factors considered include:
- The grain tightness and uniformity which indicate sound quality and durability.
- Moisture content to minimize warping or cracking over time.
- Resonance and weight, ensuring a balance between sound and playability.
Other Materials: Strings, Glue, And Varnish
Beyond wood, a classical guitar comes to life through several other materials:
- Strings:
- Nylon for rich, mellow sounds; sometimes combined with other materials for tonal variety.
- Glue:
- Animal or synthetic options used for different joints, affecting resonance and repairability.
- Varnish:
- Applied to protect the wood and enhance the guitar’s visual aesthetic.
All materials are chosen with a harmonious blend to create a classical guitar that not only plays beautifully but also stands the test of time.
Crafting The Guitar’s Body
The body of a classical guitar is like a resonant chamber, amplifying the strings’ vibrations to produce the guitar’s warm and rich sound. Expertly crafting this part of the instrument sets the stage for the exquisite melodies that classical guitars are cherished for. Let’s delve into the meticulous process of building the guitar’s body, where each component’s shape, thickness, and wood type influence the final sound.
Shaping The Soundboard
The soundboard, or the top of the guitar, is fundamental in shaping the instrument’s tone. First, luthiers select a high-quality piece of tonewood, typically spruce or cedar, prized for their resonance and flexibility. The wood must be sawn and sanded to precise thinness, balancing strength and vibrational quality.
Soundboard craftsmen then carefully shape the top, painstakingly ensuring uniform thickness to optimize sound projection. The rosette, a decorative inlay around the sound hole, is also embedded within the soundboard, adding aesthetic character as well as structural integrity.
Constructing The Sides And Back
- Bending the Sides: The sides of the guitar, slender strips of wood, usually mahogany or rosewood, are bent into the guitar’s distinctive shape. This is done using a process of heating and molding to achieve the perfect curvature.
- Joining the Sides: The two sides are joined at the neck and tail blocks, creating the guitar’s “ribs” and forming the foundation for the back and top to attach.
- Attaching the Back: Similar to the soundboard, the back piece is also shaped from tonewood, contributing to the overall tonal properties. Once prepared, it’s securely glued to the ribs.
The luthier ensures all parts align impeccably to avoid any distortion in sound.
Bracing Patterns And Resonance
Bracing, the internal framework, strengthens the guitar’s body while enhancing resonance. Used on both the soundboard and the back, the bracing pattern affects the guitar’s sound dramatically.
Bracing Type | Characteristics | Sound Influence |
---|---|---|
Fan Bracing | Traditional Spanish pattern with multiple struts fanning out from the sound hole | Delivers a balance of strength and flexibility, enhancing the tonal richness and sustain |
Lattice Bracing | Modern design consisting of a crisscross pattern | Increases projection and responsiveness, leading to a more contemporary sound |
The choice of bracing pattern is crucial — it molds the guitar’s voice and determines the balance between volume and subtlety. Upon finalizing the bracing structure, the luthier meticulously glues it in place, optimal for transmitting the string vibrations throughout the instrument.

Credit: www.yamaha.com
Neck, Fretboard, And Headstock
The neck, fretboard, and headstock are fundamental components that contribute to the feel, playability, and stability of a classical guitar. Crafting these parts requires precision, artistry, and technical knowledge, as they together form the instrument’s playing surface. From the smooth carving of the neck to the intricate installation of frets and the aesthetic design of the headstock, the creation of these elements is a blend of tradition and craftsmanship. Let’s delve into the process of how the neck, fretboard, and headstock on a classical guitar are meticulously brought to life.
Carving The Neck And Joint Construction
The neck of a classical guitar begins as a solid block of wood, often mahogany or cedar, known for their strength and lightness. The wood is carefully carved to the desired shape, ensuring a comfortable grip and the right thickness for optimal playability. The joint construction is a critical step, as it dictates the stability and alignment of the neck with the guitar’s body. A popular method employed is the Spanish heel joint, revered for its robustness. This intricate technique involves slotting the neck into the guitar’s top, offering enhanced resonance and sustain.
Fret Installation And Fretboard Material
After the neck is shaped, attention is turned to the fretboard, traditionally made from ebony or rosewood. These materials are chosen for their durability and smooth texture, facilitating ease of movement along the neck. The fretboard is glued onto the neck, providing the surface upon which the frets are installed. Installing frets demands precision – each fret wire must be cut, shaped, and positioned accurately to ensure correct intonation. The wires are pressed into the fretboard and secured in place, completing the tactile surface of the guitar’s neck.
Designing And Crafting The Headstock
The headstock is both a functional element and a canvas for decorative craftsmanship. Designing the headstock involves contouring the top of the neck wood into a shape that can hold tuning machines effectively while also displaying the luthier’s creative vision. The crafting process may include cutting the wood into a distinctive silhouette, engraving ornamental patterns, and integrating the guitar maker’s logo. Often, the aesthetics of the headstock will harmonize with the guitar’s overall design, creating a cohesive and attractive look that complements the instrument’s sound.
Assembly And Fine-tuning
The craftsmanship behind the creation of classical guitars reaches a pinnacle during the assembly and fine-tuning stage. This critical phase intertwines artistry with meticulous engineering, transitioning individual components into a cohesive, harmonious instrument. Each step, from binding to the final action adjustment, is performed with precision to ensure the guitar not only looks stunning but also produces the highest quality sound.
Binding, Gluing, And Assembling Components
The process begins with the binding of the guitar’s body, which is essential for both aesthetics and structural integrity. Binding involves attaching strips of wood or plastic to the edges of the top and back of the guitar, creating a seal that protects against damage and contributes to sound quality.
- Preparing the wood: The selection of suitable materials for the binding that complement the guitar’s aesthetics.
- Cutting channels: Precision routing around the body to accommodate the binding material.
- Application of adhesive: Using strong, musician-grade glue that ensures durability while not compromising the wood’s resonance.
Once bound, components like the neck, bridge, and fretboard are glued into position with extreme caution. The alignment of these parts dictates playability and tonal quality, making this step a careful balancing act between form and function.
Sanding, Finishing, And Varnishing
Sanding is the next crucial step, smoothing the surface and preparing the guitar for finishing. Expert hands guide the process, ensuring an even, flat surface without compromising the wood’s natural characteristics. The finishing stage includes staining or painting, followed by varnishing which protects the guitar from environmental elements and enhances its beauty.
- Grain filling: To prevent the finish from soaking into the porous wood.
- Sealing: A base coat is applied to prepare for the final finish.
- Fine sanding: Between coats, to achieve a high-quality surface for the next layer.
- Varnishing: Multiple thin coats for a durable and smooth finish.
The resulting finish is not only visually appealing but also affects the resonance and aging of the guitar.
Stringing And Action Adjustment
With the completed body and neck assembled, the guitar is ready for stringing. The choice of strings greatly influences the instrument’s tone and playability. Nylon strings, typical for classical guitars, are carefully wound around the tuning pegs, passed over the bridge, and secured.
The final stage involves precise action adjustment. Action—the distance between the strings and fretboard—determines the ease with which a musician can play the guitar. Luthiers meticulously adjust the nut and saddle for optimal string height, ensuring comfort and preventing fret buzz.
Action Components | Adjustment Process |
---|---|
Nut | Shaving the grooves to proper depth and width for each string. |
Saddle | Lowering or raising to adjust string height at the 12th fret. |
Neck | Adjusting the truss rod to fix neck relief for optimal playability. |
The finely-tuned classical guitar is a testament to a luthier’s dedication, embodying the beauty that comes from combining tradition and precision.
Quality Control And Sound Testing
Embarking on the final but critical phase of assembling a classical guitar, the journey of meticulous construction draws near completion as each instrument passes through rigorous quality control and sound testing. Ensuring that every guitar not only meets the aesthetic standards of timeless craftsmanship but also emanates the rich, melodious tones characteristic of such refined instruments, is paramount.
Inspection For Craftsmanship Defects
Each guitar is subjected to an intensive examination for craftsmanship defects. This inspection ensures that all aspects of construction adhere to the highest standards of guitar making. The process includes:
- Visual Inspection: Wood grains, finish, and overall structure analyzed for inconsistencies.
- Tactile Review: Surfaces checked for smoothness, with particular attention to the neck and fretboard.
- Structural Integrity: Bracing and joinery assessed for stability and durability.
Any identified imperfections undergo corrective measures, either through hand-finishing techniques or, in rare cases, starting anew if the flaw compromises the instrument’s integrity.
Tone And Sound Quality Assurance
The soul of a classical guitar lies in its tone and sound quality. As such, every instrument is audibly scrutinized by seasoned luthiers. Key sound parameters evaluated include:
- Balanced Tonality: Ensuring the lows, mids, and highs are harmoniously in sync.
- Volume and Projection: Testing for consistent sound output and reach.
- Sustain and Clarity: Notes must resonate clearly without premature fading.
Guitars that excel in these sound tests promise a performance-ready status, allowing musicians to express with utmost confidence.
Final Adjustments Before Distribution
Before approving any classical guitar for distribution, final adjustments are meticulously applied. This includes:
Adjustment | Details |
---|---|
Action Height | Optimizing string height for ease of playability. |
Intonation | Ensuring the guitar’s harmony at various fret positions. |
Hardware | Final check on tuning machines and bridge integrity. |
After these crucial refinements, the guitar is ready to inspire both the musician and audience with its impeccable form and resonant poetry.
The Role Of Luthiers In Guitar-making
The craftsmanship of a classical guitar is a symphony of art, science, and tradition, orchestrated by the skilled hands of a luthier. Luthiers are the heart and soul of guitar-making, transforming simple wood blocks into magnificent musical instruments. Each classical guitar narrates a story of its maker’s dedication and precise technique. As we delve deeper into this world, we’ll understand the intricate skills required to create these instruments, compare the old with the new in luthiery practices, and explore how a luthier’s unique touch influences the instrument’s sound and playability.
Skills And Techniques Of Master Luthiers
A master luthier’s artistry is evident in every curve and string of the guitar. Precision, attention to detail, and an intimate understanding of wood dynamics are paramount. Master luthiers possess skills that often span decades of experience:
- Wood Selection: Choosing the right tone wood that resonates with character and stability.
- Shaping and Bracing: Carving the wood to perfection and strategically placing braces for optimal sound projection and strength.
- Finishing: Applying natural finishes to not only protect the guitar but also to enhance its tonal qualities.
Modern Vs. Traditional Luthiery Practices
Luthiery is a profession built on tradition, yet it evolves with modern innovation. Today’s luthiers remain grounded in time-honored techniques while embracing advancements that improve precision and efficiency:
Traditional Practices | Modern Practices |
---|---|
Hand-crafted with simple tools | CNC machines for carving precision |
Manual wood bending | Thermal wood bending technology |
Glues from natural sources | Modern synthetic adhesives |
The Luthier’s Impact On Sound And Playability
The nuances a luthier introduces to a guitar are paramount, taking us beyond mere aesthetics into the realm of auditory excellence and touch sensitivity. The material choices, the way braces are contoured, and the ultimate setup—all contribute massively to the final sound and playability:
- Material Choices: Differing density and elasticity affect the guitar’s resonance and sustain.
- Brace Contouring: Altering how sound waves travel through the guitar’s body, defining its tonal signature.
- Setup: Action and intonation adjustments ensure that the guitar not only sounds good but also feels comfortable to play.
The Future Of Classical Guitar Crafting
As we step into the future, the world of classical guitar crafting is not left behind in the ever-evolving tide of innovation. For generations, the meticulous construction of classical guitars has been a testament to the artistry and craftsmanship of luthiers. Today, the fusion of time-honored techniques and cutting-edge advancements promises an exciting new chapter for both musicians and makers.
Technological Advances In Guitar-making
Recent years have seen remarkable technological strides that are transforming classical guitar production. Precision tools and computer-aided manufacturing have refined processes that were once reliant on the human hand alone.
- CNC Machines: Computer Numerical Control (CNC) machinery allows for replicable precision in carving wood for guitar components, enhancing consistency across instruments.
- 3D Printing: The advent of 3D printing offers potential for intricate inlay work and even printing entire guitar parts with unprecedented detail.
- Laser Cutting: Lasers provide immaculate cuts for intricate rosettes and fretwork, pushing the boundaries of guitar aesthetics.
With these advanced tools, luthiers can now explore design complexities and achieve results that honor both tradition and modernity.
Eco-friendly And Sustainable Practices
Sustainability now sits at the forefront of guitar-making. Amid dwindling natural resources, the search for alternative materials that align with conservation initiatives is paramount.
- Sourcing Responsibly: Wood, the soul of the guitar’s resonance, now comes from sustainably managed forests.
- Alternative Materials: Luthiers experiment with eco-friendly materials like bamboo and composites, reducing reliance on rare woods.
- Recycled Components: Embracing a circular economy, some makers repurpose old instruments or use recycled materials for parts like tuners and bridges.
The embrace of green practices not only ensures the protection of natural habitats but also secures the legacy of classical guitar crafting for generations to come.
Innovations In Classical Guitar Design
Innovation breathes new life into classical guitar design, challenging conventions while respecting the instrument’s storied heritage. Luthiers are now reimagining the classical guitar from the inside out.
Area of Innovation | Description |
---|---|
Sound Projection | Developments in bracing patterns and body dimensions offer enhanced volume and projection. |
Ergonomics | Adjustments to neck dimensions and body contours provide improved playability and comfort. |
Adjustable Features | Aiming for versatility, some guitars now feature adjustable neck angles and tension systems. |
Audacious designs and user-centric features promise to attract new players while providing seasoned guitarists with enriched dynamics and expressive possibilities.
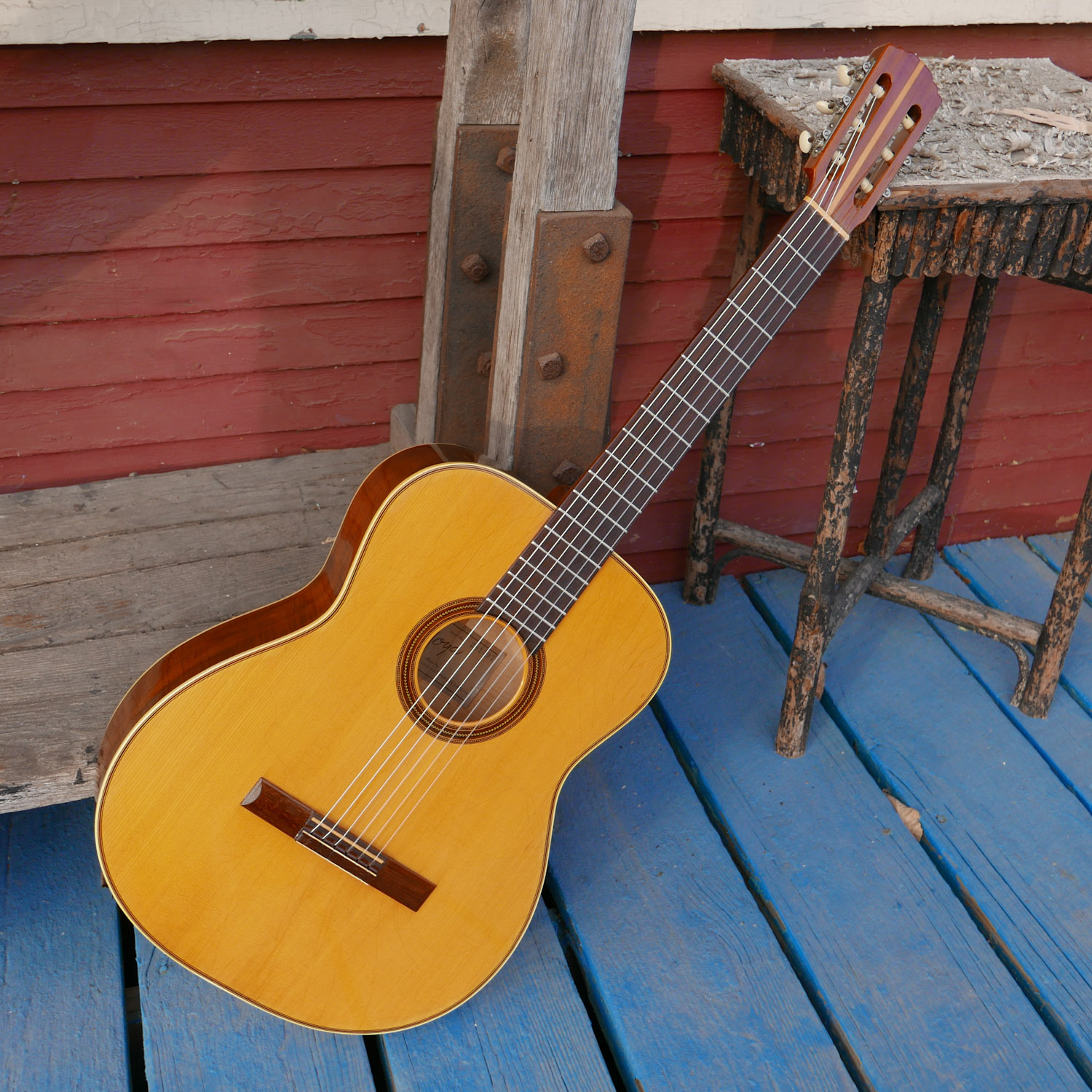
Credit: jakewildwood.blogspot.com
How Does the Manufacturing Process of Classical Guitars Compare to Taylor’s Manufacturing of Their Guitars?
The manufacturing process of classical guitars traditionally involves handcrafting each instrument, focusing on intricate wood selection and fine detailing. In contrast, the taylor classical guitar incorporates advanced technology alongside skilled artisanship, ensuring precision and consistency. This blend enhances quality while maintaining the rich tones revered in classical guitar sound.
Frequently Asked Questions For How Are Classical Guitars Made
What Are Classical Guitars Made Of?
Classical guitars typically feature tops crafted from spruce or cedar, while rosewood, mahogany, or maple form the back and sides. Ebony or rosewood is often used for the fretboard.
What Makes A Guitar A Classic?
A classic guitar typically features timeless design, high-quality materials, renowned craftsmanship, enduring popularity, and a historical significance within the music industry.
What Material Is Used For Classical Guitars?
Classical guitars typically feature tops made of spruce or cedar, with backs and sides crafted from rosewood, mahogany, or maple. Nylon strings are standard for these instruments, providing their signature soft, mellow tone.
What Makes Classical Guitar So Hard?
Classical guitar demands precise finger placement and technique, making it challenging. Complex fingerpicking patterns and comprehensive chord shapes require significant practice and dexterity. Mastery involves nuanced dynamics and tone control, adding to its difficulty.
Conclusion
Crafting classical guitars is a blend of art and precision. Each step, from selecting wood to shaping the body, reflects a luthier’s skill. These instruments are steeped in tradition, yet continually refined over time. Whether a seasoned musician or a curious enthusiast, understanding their creation deepens our appreciation for every note played.
{ “@context”: “https://schema.org”, “@type”: “FAQPage”, “mainEntity”: [ { “@type”: “Question”, “name”: “What are classical guitars made of?”, “acceptedAnswer”: { “@type”: “Answer”, “text”: “Classical guitars typically feature tops crafted from spruce or cedar, while rosewood, mahogany, or maple form the back and sides. Ebony or rosewood is often used for the fretboard.” } } , { “@type”: “Question”, “name”: “What makes a guitar a classic?”, “acceptedAnswer”: { “@type”: “Answer”, “text”: “A classic guitar typically features timeless design, high-quality materials, renowned craftsmanship, enduring popularity, and a historical significance within the music industry.” } } , { “@type”: “Question”, “name”: “What material is used for classical guitars?”, “acceptedAnswer”: { “@type”: “Answer”, “text”: “Classical guitars typically feature tops made of spruce or cedar, with backs and sides crafted from rosewood, mahogany, or maple. Nylon strings are standard for these instruments, providing their signature soft, mellow tone.” } } , { “@type”: “Question”, “name”: “What makes classical guitar so hard?”, “acceptedAnswer”: { “@type”: “Answer”, “text”: “Classical guitar demands precise finger placement and technique, making it challenging. Complex fingerpicking patterns and comprehensive chord shapes require significant practice and dexterity. Mastery involves nuanced dynamics and tone control, adding to its difficulty.” } } ] }