Putting music on a vinyl record can seem complex. But it’s simpler than you think.
First, you need to understand the process and tools involved. Vinyl records have a special charm and sound quality that digital formats can’t match. This makes them a popular choice for music lovers. Creating your own vinyl record is a great way to preserve your favorite tunes or share your music with others.
In this guide, we’ll explore the steps to put music on a vinyl record. We will cover everything from preparing your music to using the right equipment. By the end, you’ll know how to create your own vinyl records at home. Let’s dive in and bring your music to life on vinyl!
Credit: www.tiktok.com
Introduction To Vinyl Records
Vinyl records have a special place in music history. They are cherished for their unique sound quality and nostalgic value. Many music lovers still prefer the warmth of vinyl records over digital formats.
Brief History
The journey of vinyl records began in the early 20th century. Thomas Edison created the phonograph in 1877, which could record and reproduce sound. Later, Emile Berliner developed the gramophone, using flat discs instead of cylinders.
By the 1940s, vinyl records became the standard for music playback. They offered better sound quality and durability. The 33 1/3 RPM LP (Long Play) and the 45 RPM single became popular formats.
Vinyl records ruled the music industry until the 1980s, when CDs took over. Yet, vinyl never completely disappeared.
Popularity Resurgence
In recent years, vinyl records have seen a significant comeback. Music enthusiasts appreciate the tangible experience of handling a vinyl record. The large album art and liner notes add to the appeal.
Many new artists are releasing their music on vinyl. This trend is driven by the desire for authentic sound and the physical connection to music. In 2020, vinyl sales surpassed CD sales for the first time in decades.
Collectors and audiophiles seek out rare and vintage records. This has created a vibrant market for both new and used vinyl records.
In conclusion, vinyl records hold a timeless charm. They continue to attract new generations of music lovers.

Credit: vinylify.com
Necessary Equipment
To transfer music onto a vinyl record, you need specific equipment. The process involves more than just playing music. You need tools to cut and inscribe the sound into the vinyl. Let’s explore the necessary equipment.
Turntables
Turntables are essential for playing vinyl records. They rotate the record at a constant speed. This ensures the music sounds correct. There are various types of turntables. Direct-drive turntables are common in DJ setups. Belt-drive turntables are often used at home. Each type has its benefits. The choice depends on your needs.
Cutting Lathes
Cutting lathes are crucial for making vinyl records. They cut grooves into the vinyl. These grooves store the music. Cutting lathes use a sharp needle. This needle moves according to the music’s sound waves. It creates precise patterns in the vinyl. This process is delicate. It requires skill and precision. Proper use ensures high-quality sound on the final record.
Preparing The Music
Before you can put music on a vinyl record, you need to prepare your music properly. This step is crucial to ensure your vinyl sounds great. Preparing the music involves paying close attention to audio quality and mastering the track.
Audio Quality
Start with the highest quality audio file. Vinyl records capture every detail. Poor quality files will lead to poor vinyl sound. Use lossless audio formats like WAV or FLAC. These formats retain all the audio data. Avoid compressed formats like MP3. They lose a lot of audio detail.
Listen to your track carefully. Make sure there are no unwanted noises. Hisses, pops, and clicks should be removed. These sounds will be more noticeable on vinyl. Use audio editing software to clean up your track. This step ensures a clear and crisp sound on your vinyl.
Mastering The Track
Mastering is the final step before pressing. It makes sure your music sounds its best. Vinyl records have unique sound characteristics. Your track needs special adjustments for vinyl. This process is called vinyl mastering.
Adjust the volume levels. Vinyl has a limited dynamic range. Keep the volume consistent. Avoid sudden loud peaks. These can cause distortion. Also, manage the bass frequencies. Too much bass can make the needle jump. Use an equalizer to balance the sound.
Consider hiring a professional mastering engineer. They have the skills and tools for the best results. They will make sure your track is vinyl-ready. This investment ensures your vinyl record sounds amazing.
Cutting The Vinyl
Ever wondered how music gets onto a vinyl record? The process is both technical and artistic. One crucial step in this journey is cutting the vinyl. This stage involves translating audio files into physical grooves on the vinyl surface. Let’s dive into the key elements of this fascinating process.
Creating The Master Disc
The first step in cutting the vinyl is creating the master disc. This disc acts as the original template for all subsequent copies. It is made from a material like lacquer-coated aluminum. The audio is transferred to this disc using a cutting lathe.
The lathe cuts grooves into the disc. These grooves represent the sound waves. Engineers monitor the process closely to ensure high fidelity. Any mistakes here will affect the final product. Thus, precision is key.
Lacquering Process
After creating the master disc, the next step is the lacquering process. This process involves coating the disc with a thin layer of lacquer. The lacquer protects the grooves and ensures the audio quality remains intact.
The lacquered disc is then inspected for any imperfections. Technicians use specialized tools to check for any errors. Any flaw can ruin the audio quality, so this step is critical. Once approved, the disc is ready for the next phase.
Pressing The Record
Creating a vinyl record is an art and science. The process starts with pressing the record. This step is crucial to ensure high-quality sound. It involves several stages, each vital to the final product.
Stampers Creation
The first step in pressing a record is creating the stampers. Stampers are metal plates used to press the vinyl. They are made from the master lacquer. This lacquer is a smooth disc coated with a photoresist layer.
Engraving the audio onto the master lacquer is done using a lathe. This lathe cuts grooves into the lacquer. Each groove represents the sound wave of the music. Once the master lacquer is complete, it undergoes electroforming. This process creates a negative mold called the “mother.” From this mother, the stampers are made.
Vinyl Pressing Process
With stampers ready, the vinyl pressing process begins. The vinyl pressing process involves several steps:
- Heating the Vinyl: Vinyl pellets are heated until they become a thick paste.
- Placing the Vinyl: This paste is placed between two stampers.
- Pressing the Vinyl: The stampers press the paste into the shape of a record.
- Cooling the Record: The pressed vinyl is cooled to harden it.
After cooling, the excess vinyl around the edges is trimmed. The result is a finished vinyl record. This record undergoes quality checks to ensure it meets standards.
This process ensures each record has the best possible sound. Vinyl records are not just about music; they are a piece of art.
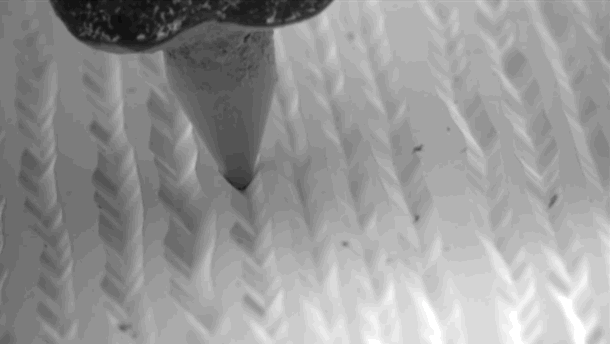
Credit: www.londonsoundacademy.com
Quality Control
Quality control is crucial in the vinyl record production process. It ensures the final product meets high standards. This process involves several steps. Each step focuses on detecting and correcting errors.
Test Pressings
The first step in quality control is the test pressing. This step involves creating a small batch of records. These records are thoroughly checked for any defects. Engineers listen to these test pressings. They check for audio quality. They listen for pops, clicks, and other noises. The goal is to identify and fix issues before mass production starts.
Final Inspection
The final inspection is the last step in the quality control process. Each record is checked one last time. Inspectors look for any visual defects. They check the surface for scratches or warps. They also verify the labels are correctly placed. This step ensures every record meets the highest standards before reaching the customer.
Packaging The Vinyl
Packaging the vinyl is a crucial step. It protects your record and showcases its aesthetic appeal. Good packaging can make your vinyl stand out. This section will guide you through the essentials.
Sleeve Design
The sleeve design is the first thing someone sees. It represents the music inside. Think about the artwork and information you want on the sleeve. Use high-quality images and print. This will attract listeners.
Include the album title and artist name prominently. You can also add a tracklist on the back. Make sure the font is readable. Choose colors that complement each other. A well-designed sleeve adds value to your vinyl.
Protective Packaging
Protective packaging is essential to keep the vinyl safe. Use an inner sleeve made of anti-static material. This prevents dust and scratches. The outer sleeve should be sturdy and durable.
Consider adding a plastic outer cover. This adds an extra layer of protection. It also keeps the sleeve clean. A well-protected vinyl will last longer.
Packaging Component | Purpose |
---|---|
Inner Sleeve | Prevents dust and scratches |
Outer Sleeve | Provides a sturdy cover |
Plastic Outer Cover | Adds extra protection |
In summary, packaging the vinyl involves careful design and protection. Focus on the sleeve design and protective packaging to ensure the vinyl is both attractive and safe.
Maintaining Vinyl Records
Maintaining vinyl records is essential to keep your music sounding great. Proper care prevents damage and ensures longevity. Let’s explore some key aspects of maintaining vinyl records.
Proper Storage
Store records vertically to avoid warping. Use sturdy shelves or crates. Ensure the space is cool and dry. Avoid direct sunlight to prevent damage. Use inner sleeves to protect from dust. Invest in outer sleeves for extra protection.
Cleaning Techniques
Clean records before and after each play. Use a carbon fiber brush to remove surface dust. For deeper cleaning, use a record cleaning solution. Gently wipe in a circular motion. Avoid harsh chemicals to prevent damage. Dry records completely before storage.
Frequently Asked Questions
What Equipment Do You Need To Make A Vinyl Record?
To make a vinyl record, you need a vinyl cutter, blank vinyl discs, and audio source equipment.
How Long Does It Take To Press A Vinyl Record?
Pressing a vinyl record can take anywhere from a few hours to a few days, depending on the complexity.
Can You Put Digital Music On Vinyl?
Yes, digital music can be converted and pressed onto vinyl records using specialized equipment and software.
Is It Expensive To Press Your Own Vinyl?
Pressing your own vinyl can be costly, with prices ranging from hundreds to thousands of dollars, depending on quantity.
Conclusion
Creating your own vinyl record can be a fun process. With the right tools and guidance, anyone can do it. Remember to choose your music carefully. Ensure your equipment is set up correctly. Take your time during the recording phase.
Enjoy the unique experience of hearing your favorite tracks on vinyl. This process may seem complex, but practice makes it easier. Start small and build your skills. Soon, you’ll enjoy the warm, rich sound of your own vinyl records. Happy recording!
{ “@context”: “https://schema.org”, “@type”: “FAQPage”, “mainEntity”: [ { “@type”: “Question”, “name”: “What equipment do you need to make a vinyl record?”, “acceptedAnswer”: { “@type”: “Answer”, “text”: “To make a vinyl record, you need a vinyl cutter, blank vinyl discs, and audio source equipment.” } } , { “@type”: “Question”, “name”: “How long does it take to press a vinyl record?”, “acceptedAnswer”: { “@type”: “Answer”, “text”: “Pressing a vinyl record can take anywhere from a few hours to a few days, depending on the complexity.” } } , { “@type”: “Question”, “name”: “Can you put digital music on vinyl?”, “acceptedAnswer”: { “@type”: “Answer”, “text”: “Yes, digital music can be converted and pressed onto vinyl records using specialized equipment and software.” } } , { “@type”: “Question”, “name”: “Is it expensive to press your own vinyl?”, “acceptedAnswer”: { “@type”: “Answer”, “text”: “Pressing your own vinyl can be costly, with prices ranging from hundreds to thousands of dollars, depending on quantity.” } } ] }