Making an acoustic guitar is a highly skilled and complex task that requires expert craftsmanship and years of experience. It is a labor-intensive process that involves various steps such as selecting high-quality wood, shaping the body, assembling parts, and fine-tuning the instrument.
This meticulous process demands precision, knowledge of woodworking techniques, and a deep understanding of acoustics. From shaping the neck to installing the frets and bridge, each step requires careful attention to detail. In addition, the process involves the use of specialized tools and equipment.
Due to these factors, making an acoustic guitar is considered a challenging and time-consuming endeavor.
The Craftsmanship Involved In Guitar Making
When it comes to making an acoustic guitar, the craftsmanship involved is truly remarkable. Each guitar is handcrafted by skilled artisans who painstakingly construct every component, ensuring that every detail is perfect. From selecting the finest woods to the intricate art of guitar making, the level of skill and dedication required to produce a high-quality acoustic instrument is unparalleled. In this article, we will explore the various aspects of guitar making that make it such a challenging but fulfilling craft.
The Intricate Art of Guitar Making
Mastering the woodworking skills necessary for guitar making is no small feat. An experienced craftsman must possess a deep understanding of different types of woods and their tonal qualities. Careful consideration is given to the selection and combination of woods for the guitar body, neck, and fingerboard to achieve the desired tone and resonance.
Moreover, the shaping and carving of the guitar body require precision and attention to detail. Every curve, angle, and contour must be carefully carved to optimize both the aesthetics and sound of the instrument. The craftsmanship involved in creating the perfect body shape is truly an art form in itself.
Mastering the Woodworking Skills
The woodworking skills required to make an acoustic guitar are extensive and require years of practice to master. From joining the guitar top and back plates with delicate bracing to crafting the neck joint for optimal stability, each step in the process must be executed with precision.
Guitar makers must also possess exceptional knowledge of woodworking tools and techniques. From using chisels and hand planes to carve the intricate details of the fretboard, to employing specialized jigs and clamps to ensure accurate assembly, the mastery of these skills is crucial to producing a high-quality instrument.
In addition, the art of guitar finishing is another aspect that demands meticulous attention. Applying the perfect combination of stains, dyes, and clear coats to the guitar’s wood surface requires skillful application and a keen eye for detail. The finish not only enhances the visual appeal but also protects the wood and contributes to the overall tonal characteristics of the instrument.
Ensuring Each Guitar is a Masterpiece
Throughout the entire guitar making process, every step is taken to ensure that each instrument is a masterpiece. From meticulously matching the grain patterns of the wood to crafting custom inlays on the fretboard, guitar makers go above and beyond to create unique and visually stunning instruments.
Furthermore, rigorous quality control measures are implemented to ensure that each guitar meets the highest standards. String tensions, intonation, and playability are carefully assessed and fine-tuned, guaranteeing that every instrument that leaves the workshop is not only beautiful but also a joy to play.
Overall, the craftsmanship involved in guitar making is a testament to the dedication, skill, and passion of the artisans who create these musical works of art. From the selection and combination of fine woods to the precise woodworking techniques and finishing touches, every step in the process plays a crucial role in producing a high-quality, resonant, and visually striking acoustic guitar.
Essential Tools And Materials For Guitar Making
When it comes to making an acoustic guitar, having the right tools and materials is essential to ensure a high-quality final product. The process of guitar making requires precision and attention to detail, making it crucial to select the necessary tools and high-quality materials that will result in the best possible outcome. In this article, we will explore the necessary tools for the job and the importance of selecting high-quality materials.
Exploring the necessary tools for the job
Before embarking on the journey of making an acoustic guitar, it is essential to gather the necessary tools. These tools will help you shape the wood, attach the guitar components, and achieve the desired sound. Here are some of the tools you will need:
- A bracing chisel: This tool is used to shape and carve the braces that provide structural support to the guitar’s soundboard.
- A fret saw: This saw is specifically designed for cutting fret slots on the guitar’s fingerboard.
- A radius dish: This tool is used to create the curved shape of the guitar’s top and back.
- A bending iron: This tool is crucial for bending the sides of the guitar to achieve the desired shape.
- A flush-cutting saw: This saw is used for trimming excess materials and achieving clean edges.
- A truss rod wrench: This wrench is necessary for adjusting the truss rod, which helps control the guitar’s neck relief.
These are just a few examples of the tools that you will need for guitar making. Each tool serves a specific purpose and contributes to the overall construction process, ensuring that your acoustic guitar turns out to be a true work of art.
Selecting high-quality materials for the best results
When it comes to the materials used in guitar making, selecting high-quality options is paramount. The choice of wood, in particular, plays a crucial role in determining the tone, resonance, and overall quality of the instrument. Here are some high-quality woods often used in guitar making:
Wood Type | Main Usage |
---|---|
Spruce | Soundboard |
Mahogany | Neck and back/sides |
Rosewood | Fingerboard and bridge |
Maple | Neck and back/sides |
By selecting high-quality woods such as spruce, mahogany, rosewood, and maple, you can ensure that your acoustic guitar produces a rich and vibrant sound.
In conclusion, having the essential tools and using high-quality materials are vital components of making a remarkable acoustic guitar. The tools enable you to shape and assemble the instrument, while the materials determine the overall tone and resonance. By carefully selecting the necessary tools and opting for high-quality woods, you are well on your way to crafting a truly exceptional acoustic guitar.
Step-By-Step Process Of Making An Acoustic Guitar
Making an acoustic guitar is a meticulous process that requires thorough attention to detail and expert craftsmanship. From designing the guitar body and neck to assembling and attaching the various parts, each step plays a crucial role in creating a high-quality instrument. In this article, we will dive into the step-by-step process of making an acoustic guitar, exploring the intricate tasks involved in bringing this beautiful musical instrument to life.
Designing the guitar body and neck
The first step in making an acoustic guitar is designing the body and neck. This process involves creating a blueprint or template of the guitar shape, considering factors such as tone, playability, and aesthetics. The body shape influences the sound and projection of the guitar, while the neck design affects the playability and comfort for the musician. Expert luthiers carefully sculpt the body and neck to achieve the desired balance and feel.
Constructing the guitar bracing
Once the body and neck design is finalized, the next step is constructing the guitar bracing. Bracing is essential for reinforcing the guitar’s top and back, enhancing its structural integrity and influencing its sound. This process involves carefully carving and shaping wooden braces that are strategically placed inside the guitar body. The placement and thickness of these braces greatly affect the guitar’s tone, resonance, and durability.
Shaping and carving the guitar components
After the bracing is complete, the luthier moves on to shaping and carving the various guitar components. This includes crafting the soundboard (top), back, and sides of the guitar. Using specialized tools, the luthier meticulously carves and shapes these wooden pieces to precise measurements and contours. This step is crucial in achieving optimal sound projection, tonal balance, and visual appeal.
Assembling and attaching the guitar parts
Once all the guitar components are shaped and carved, it’s time to assemble and attach them. This includes carefully fitting the neck into the body, attaching the sides to the top and back, and securing the fretboard and bridge. Each joint and connection must be precise to ensure proper alignment and structural stability. The luthier meticulously glues, clamps, and reinforces these parts to create a durable and resonant instrument.
To add to the guitar’s functionality and aesthetics, the luthier may also install additional features such as bindings, inlays, and decorative elements. These final touches enhance the instrument’s visual appeal and make it a unique work of art.
Creating an acoustic guitar is a labor-intensive process that demands skill, patience, and attention to detail. From designing the body and neck to shaping and assembling the various components, each step contributes to the creation of a harmonically rich and visually stunning instrument. Whether you are a musician or simply appreciate the beauty of these instruments, understanding the step-by-step process of making an acoustic guitar adds a new level of appreciation for these masterpieces.
Dealing With Woodworking Challenges
Introduction: Dealing with Woodworking Challenges
When it comes to creating an acoustic guitar, one of the biggest challenges lies in the woodworking process. Working with different types of wood, managing wood deformation and moisture issues are some of the key aspects that guitar makers need to tackle. These challenges require skill, precision, and an understanding of the properties of wood. In this article, we will delve into the intricacies of dealing with these woodworking challenges and explore the techniques employed by expert luthiers to ensure the quality and durability of acoustic guitars.
Working with different types of wood
Acoustic guitars are typically crafted using a variety of woods, each carefully chosen for its unique properties. Different woods offer distinct tonal characteristics, resonance, and durability. Let’s take a closer look at some popular woods used in guitar making:
Wood Type | Tonal Characteristics | Common Use |
---|---|---|
Spruce | Bright, responsive, balanced | Soundboards (top) |
Mahogany | Warm, rich, focused | Back and sides |
Rosewood | Deep, complex, full-bodied | Fingerboards, bridges |
Maple | Bright, punchy, articulate | Necks |
Working with each type of wood requires a different approach. For instance, spruce is a popular choice for soundboards due to its responsiveness, but it needs to be handled delicately to prevent cracking. On the other hand, mahogany, known for its durability, requires precision cutting to bring out its warm and focused tones. Understanding the characteristics of different woods and how they contribute to the overall sound of the guitar is crucial for guitar makers.
Managing wood deformation and moisture issues
Wood is a natural material that can be influenced by environmental factors such as humidity and temperature. It has the tendency to deform, shrink, or expand, which can affect the structural integrity of an acoustic guitar. Luthiers employ various techniques to tackle these challenges:
- Wood selection: Choosing well-seasoned and properly dried wood is paramount. This helps minimize the risk of deformation and ensures stability.
- Humidity control: Luthiers use humidity-controlled environments to store and work with wood. This helps maintain consistent moisture levels, reducing the chances of warping or cracking.
- Bracing techniques: Internal bracing plays a crucial role in reinforcing the guitar’s body and preventing excessive deformation. The design and placement of braces are carefully considered to provide strength without hindering the resonance of the instrument.
- Finish application: Applying a protective finish to the guitar’s exterior helps seal the wood and minimize moisture absorption. This further aids in preventing warping or swelling due to changes in environmental conditions.
By implementing these strategies, luthiers are able to address the challenges posed by wood deformation and moisture, ensuring the longevity and performance of the acoustic guitar.
Overcoming Structural And Design Challenges
When it comes to making an acoustic guitar, one of the most significant challenges faced by luthiers is overcoming the structural and design hurdles. From ensuring the proper bracing and support for sound projection to achieving the desired tonal characteristics, creating a high-quality acoustic guitar involves meticulous attention to detail and craftsmanship. Let’s delve into these challenges and explore how luthiers overcome them.
Ensuring the proper bracing and support for sound projection
One of the key factors that contribute to the exceptional sound quality of an acoustic guitar is the bracing. Proper bracing not only provides structural support to the guitar but also plays a vital role in sound projection and resonance. Luthiers carefully design and position the bracing patterns to optimize the tonal characteristics of the instrument.
Typically, acoustic guitars feature two main types of bracing patterns: X-bracing and fan bracing. X-bracing involves two braces forming an ‘X’ shape beneath the soundboard, enhancing the guitar’s sustain and volume. On the other hand, fan bracing utilizes a network of braces arranged like a fan, distributing the sound energy more evenly across the soundboard and delivering a rich tonal palette.
In addition to the bracing pattern, luthiers meticulously shape and carve the braces to achieve the desired sound projection and tonal balance. The thickness, height, and curvature of the braces are carefully calculated to ensure optimal resonance and structural stability. Attention to these minute details leads to the creation of an acoustic guitar that not only looks exquisite but also produces a captivating and resonant sound.
Achieving the desired tonal characteristics
Every guitarist has a unique preference when it comes to the tonal characteristics of their instrument. Some may seek a bright and crisp sound, while others may prefer a warm and mellow tone. Achieving the desired tonal characteristics in an acoustic guitar requires a delicate balancing act between various factors such as the choice of tonewoods, body shape, and bracing.
First and foremost, the selection of tonewoods is crucial in determining the tonal qualities of an acoustic guitar. Luthiers carefully choose the top (soundboard) and back and sides of the guitar, considering factors such as density, stiffness, and resonant properties of the wood. Different wood combinations produce distinct tonal profiles and harmonics, allowing luthiers to cater to different playing styles and genres.
Furthermore, the body shape of the guitar significantly influences the sound projection and tonality. Whether it’s a dreadnought, concert, or jumbo, each body shape has its unique characteristics, affecting factors like volume, bass response, and midrange emphasis. Luthiers experiment and refine their designs to strike a perfect balance between form and function, creating guitars that not only look visually appealing but also produce the desired tonal qualities.
In conclusion, crafting an acoustic guitar involves overcoming various structural and design challenges. From ensuring proper bracing for sound projection to achieving the desired tonal characteristics, luthiers pour their expertise and passion into each instrument they create. Through meticulous craftsmanship and attention to detail, they create guitars that delight musicians with their exceptional sound quality and tonal versatility.
Finishing And Polishing The Guitar
Finishing and polishing the guitar is a critical step in the journey of making an acoustic guitar. This is where the true beauty of the instrument starts to shine as the finishing touches are applied. The process involves applying a flawless finish and then polishing the guitar to achieve a professional look. Let’s take a closer look at each step.
Applying a Flawless Finish
Applying a flawless finish is an art form in itself. It involves carefully coating the guitar’s body, neck, and headstock with the chosen finish, be it lacquer, varnish, or shellac. Each type of finish has its own unique qualities, and the choice depends on the desired aesthetic and tonal characteristics.
However, regardless of the type of finish, the process typically involves multiple thin coats. This ensures that the finish is smooth, even, and adds depth and protection to the wood. The application process requires precision and attention to detail, as any imperfections or unevenness can significantly impact the visual appeal and resonance of the guitar.
To achieve a flawless finish, several techniques are employed. One common method is spray finishing, where the finish is evenly sprayed onto the guitar’s surface using specialized equipment. Another approach is hand-rubbing the finish, which involves meticulously applying thin layers and using soft materials to achieve a smooth surface. Regardless of the technique, patience and skill are essential to achieving a flawless finish.
Polishing the Guitar for a Professional Look
Once the finish has been applied, the next step is polishing the guitar to give it a professional look. Polishing not only enhances the beauty of the wood but also smooths out any imperfections, and provides protection against wear and tear.
There are several methods and materials used for guitar polishing, depending on the type of finish applied. One common approach is using polishing compounds or pastes. These products contain fine abrasives that help remove any scratches, swirl marks, or dullness from the finish surface.
Polishing can be done by hand using a soft cloth or with the help of a buffing wheel attached to a rotary tool. The goal is to gently buff the surface in circular motions, gradually revealing the guitar’s lustrous finish. This process requires careful attention to avoid applying excessive pressure, which can damage the finish or alter the shape of the guitar.
Once the polishing is complete, a final step involves applying a guitar wax or polish to protect the finish and maintain its shine for years to come. This step not only adds a layer of protection but also brings out the depth and brilliance of the finish, giving the guitar a professional, showroom-worthy appearance.
In Conclusion
The finishing and polishing stage of making an acoustic guitar is a labor-intensive process, requiring precision, patience, and skill. By diligently applying a flawless finish and expertly polishing the guitar, luthiers can transform a raw wooden instrument into a work of art. The final result is an acoustic guitar that not only sounds beautiful but also looks stunning, ready to be played and cherished for years to come.
The Joy Of Creating A Musical Instrument From Scratch
For music enthusiasts and craftsmen alike, there is a profound joy in the process of creating a musical instrument from scratch. In an age of mass production and instant gratification, the art of handcrafting an acoustic guitar holds a special place. From selecting the finest tonewoods to painstakingly shaping and refining each component, every step is filled with a sense of dedication, passion, and attention to detail.
The satisfaction of seeing your hard work pay off
There is a deep satisfaction that comes from watching your hard work and dedication transform into a beautiful, functioning instrument. As you meticulously handcraft each part, investing countless hours into shaping the body, carving the neck, and assembling the intricate components, you can’t help but feel a sense of pride and accomplishment with each milestone achieved. The process of creating an acoustic guitar is not for the faint of heart; it requires a steady hand, a discerning eye, and an unwavering commitment to excellence. But when you finally string up the guitar for the first time, pluck a chord, and hear the harmonious resonance fill the room, all the effort and perseverance become worth it.
The pride of playing an instrument you made yourself
There is a unique pride that comes from playing an instrument you made with your own hands. Knowing that every note and melody that emanates from its strings is a result of your craftsmanship is an unmatched feeling. Each strum becomes a testament to your skill, dedication, and creativity. Whether you are playing in front of an audience, jamming with friends, or practicing alone, the intimate connection between you and your handcrafted guitar becomes palpable. The instrument becomes an extension of yourself, reflecting your style and personality in its tones. Hearing the rich sounds you have created provides a deep satisfaction that goes beyond mere enjoyment; it is a reminder of what can be accomplished with passion and dedication.
The Learning Experience And Personal Growth
Learning how to make an acoustic guitar is not just a matter of acquiring a new skill. It is an immersive and transformative journey that encompasses personal growth and development. The process of crafting an instrument from scratch teaches valuable lessons that extend far beyond the realm of guitar making itself.
Developing new skills and knowledge in guitar making
When embarking on the journey of making an acoustic guitar, you delve into a world of craftsmanship that requires you to develop a host of new skills and acquire in-depth knowledge. From shaping the body and neck to crafting a soundboard and installing the bracing, every step of the process demands precision and expertise.
This hands-on experience allows you to expand your knowledge of woodworking, familiarize yourself with different types of tonewoods, and gain insights into the intricacies of instrument construction. As you research, practice, and learn from experienced luthiers, you become well-versed in the art of guitar making, enriching your understanding of the instrument as a whole.
Overcoming challenges and gaining confidence in craftsmanship
Throughout the guitar making process, you are bound to encounter numerous challenges and obstacles that test your patience and problem-solving abilities. From initial measurements to the final finishing touches, every aspect of crafting an acoustic guitar involves intricate details that require meticulous care and attention.
By navigating through these challenges, you gradually develop a sense of confidence in your craftsmanship. Each successfully completed task reinforces your belief in your abilities and propels you further on your journey. You learn to troubleshoot, adapt to unexpected situations, and refine your techniques, ultimately becoming a skilled artisan in the realm of guitar making.
This newfound confidence extends beyond the workshop. As you witness your skills and craftsmanship improve, you cultivate a sense of self-assurance that carries over into other aspects of your life. The ability to overcome challenges and achieve tangible results fosters a growth mindset and instills a belief that you can tackle any obstacle that comes your way.
Developing new skills and knowledge in guitar making | Overcoming challenges and gaining confidence in craftsmanship |
---|---|
|
|
Sharing Your Craftsmanship With Others
Building an acoustic guitar requires exceptional skill, precision, and perseverance. It is a labor of love that yields a beautiful instrument capable of producing mesmerizing melodies. But what if you could take your passion for guitar making a step further and share your craftsmanship with others? The joy of impressing others with your handcrafted guitar and exploring potential opportunities for selling or customizing guitars for fellow musicians is incomparable. Let’s delve into these exciting possibilities and see how you can bring your love for guitar making to a wider audience.
Impressing others with your handcrafted guitar
There’s something truly magical about showcasing a handcrafted acoustic guitar to fellow musicians, friends, and family. The hours spent carefully selecting the wood, shaping the body, and finishing every minute detail come to life in the mesmerizing tones that emanate from the strings. Each step of the process, from hand carving the neck to intricately placing the frets, reflects your mastery of the craft and provides a unique opportunity to impress others with your dedication, talent, and attention to detail.
Not only does your handcrafted guitar serve as a testament to your woodworking skills, but it also becomes a conversation piece. Musicians and enthusiasts alike will be drawn to the instrument’s beauty and unparalleled sound, prompting discussions about the craft behind it. This opens a world of possibilities for connecting with like-minded individuals, forging new friendships, and even collaborating on musical projects. Remember, the guitar you’ve meticulously created has the power to captivate not just through its music but also through the story it carries.
Potential opportunities for selling or customizing guitars for others
As your reputation as a guitar maker grows, so too will the interest from fellow musicians seeking extraordinary instruments. The demand for custom-made acoustic guitars with exceptional tone, craftsmanship, and unique aesthetic qualities is always present in the music community. By sharing your expertise with others, you can open doors to potential opportunities for selling or customizing guitars for musicians who value the artistry and soul that goes into handcrafted instruments.
Customizing guitars can involve creating bespoke designs, incorporating personalized touches, or tailoring the instrument to match a musician’s preferences and playing style. This enables you to create instruments that are not only functional but also deeply meaningful to the individuals who will perform with them. The satisfaction of delivering an instrument that surpasses expectations and resonates harmoniously with the player’s musical journey adds an element of fulfillment to your craft.
Furthermore, selling your handcrafted guitars can not only provide financial rewards but also enable others to experience the exceptional quality and artistry you’ve poured into your work. Whether it’s through word-of-mouth recommendations or establishing an online presence, you can attract potential buyers who appreciate the inherent value of a handcrafted acoustic guitar. Building a reputation as a trusted luthier creates opportunities for growth and widens your reach, allowing you to touch the lives of musicians around the world.
Beyond the monetary or career benefits, sharing your craftsmanship with others connects you to a community of musicians who deeply appreciate the commitment and passion that go into creating an acoustic guitar. Together, you strengthen the legacy of this timeless instrument and perpetuate the beauty of handcrafted music in a world driven by mass production and digital technology. So, embrace the opportunity to share your talent with the world and watch as your handcrafted guitars resonate with musicians in a way that only true art can.
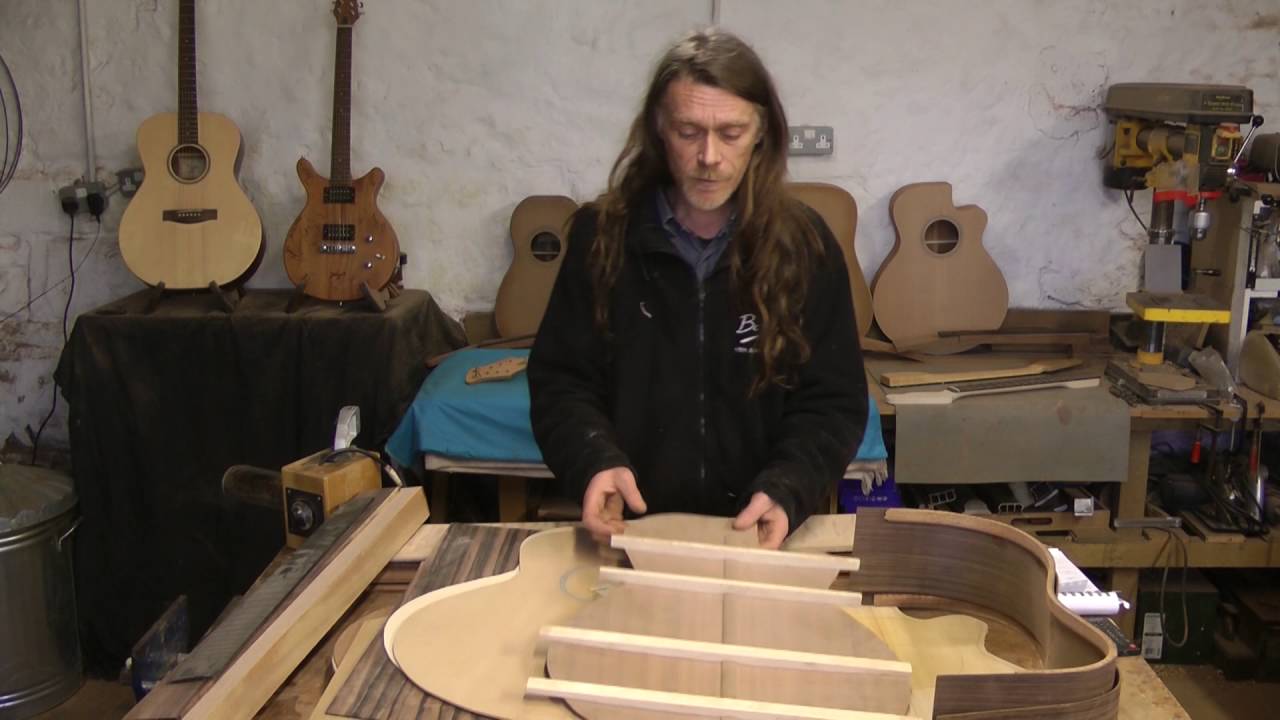
Credit: www.youtube.com
Is Understanding How Semi-Acoustic Guitars Work Helpful for Making an Acoustic Guitar?
Understanding semiacoustic guitars reveals valuable insights into acoustic sound projection and design. These instruments blend electric and acoustic features, highlighting the importance of resonance and amplification. By grasping the mechanics involved, one can apply these principles to enhance the craftsmanship of an acoustic guitar, leading to richer tones and improved performance.
Frequently Asked Questions On How Hard Is It To Make An Acoustic Guitar
How Long Does It Take To Build An Acoustic Guitar?
Building an acoustic guitar usually takes several weeks to several months, depending on the complexity of the design and the experience of the builder.
Is It Cheaper To Build An Acoustic Guitar?
Building an acoustic guitar can be cheaper compared to buying one, as it eliminates the cost of brand markup. However, the total cost depends on factors like materials, tools, and skills required for construction.
How Hard Is It To Make A Guitar?
Making a guitar can be challenging, but it’s not impossible. It requires skill, patience, and knowledge about the materials and tools needed for the process. With proper guidance, anyone can learn to build their own guitar.
How Much Does It Cost To Build A Guitar From Scratch?
Building a guitar from scratch costs around $500 to $3000, depending on the quality of materials and customization desired.
Conclusion
Crafting an acoustic guitar may seem daunting, but with the right skills and resources, it’s an achievable feat. The process involves meticulously selecting materials, shaping and assembling components, and fine-tuning the instrument. While it may require patience and dedication, the joy of creating a beautiful and harmonious guitar is unparalleled.
So, why wait? Embrace this rewarding craft and embark on your journey to making your own acoustic guitar today.