A bass guitar is crafted through a meticulous process of shaping the body, neck, and headstock, followed by installing hardware and electronics. Luthiers select quality woods and materials, cut the shapes, and assemble the components for a finished instrument.
The creation of a bass guitar is an intersection of artistry and precision, where skilled artisans called luthiers bring musical tools to life. Crafting a bass guitar involves selecting tonewoods like maple or mahogany for their sonic properties and resilience.
These woods form the guitar’s foundation—the body provides the resonance while the neck sets the stage for playability. Luthiers use advanced machinery and hand tools to intricately shape, sand, and finish each part, ensuring both visual appeal and comfort for the player. Hardware such as tuning pegs, bridge, pickups, and controls are then carefully installed, each contributing to the instrument’s overall tone and functionality. Finally, strings are added, and the guitar is fine-tuned, giving musicians the power to produce those iconic deep tones that anchor the rhythm and harmony in music. With every crafted bass guitar, there arises a new possibility for creative expression, showcasing the harmonious blend of craftsmanship and technology in modern instrument-making.

Credit: www.youtube.com
Introduction To The Bass Guitar
The bass guitar stands as a cornerstone of modern music, laying the foundation for rhythm and harmony across genres. This powerful instrument brings depth and groove to musical compositions, accentuating the low-frequency spectrum that captivates listeners. Its strings vibrate to produce resonant tones, essential for creating a full and balanced sonic experience.
The Role and Importance of the Bass Guitar in MusicThe Role And Importance Of The Bass Guitar In Music
The bass guitar plays a pivotal role in music. With its low-end rumble, it serves as the backbone of a band’s sound. Let’s dive into its key functions:
- Rhythmic Stability: The bass guitar provides a steady tempo, working closely with the drums to lock in the beat.
- Harmonic Framework: It outlines the chord structure of a song, guiding the harmony and supporting other instruments.
- Dynamic Power: With its robust sound, the bass adds energy and intensity to a track, driving the music forward.
Its significance extends beyond mere sound; the bass induces a palpable physical sensation, often felt as much as it is heard. This unique characteristic makes it an undisputed force in music.
Brief History of the Bass GuitarBrief History Of The Bass Guitar
The evolution of the bass guitar is fascinating. Originating from the upright double bass, the bass guitar underwent transformation for greater playability and accessibility. Here is a snapshot of its journey:
Year | Development |
---|---|
1930s | Early adaptations of fretted basses appear. |
1951 | Leo Fender introduces the Precision Bass, a game-changer in bass guitar history. |
1960s and Beyond | Further advancements lead to diverse designs, amplified tones and the rise of iconic models. |
From the vintage, woody timbres of classic rock to the punchy, synthesized lines of modern pop, the bass guitar’s adaptability has cemented its place across musical styles and eras.
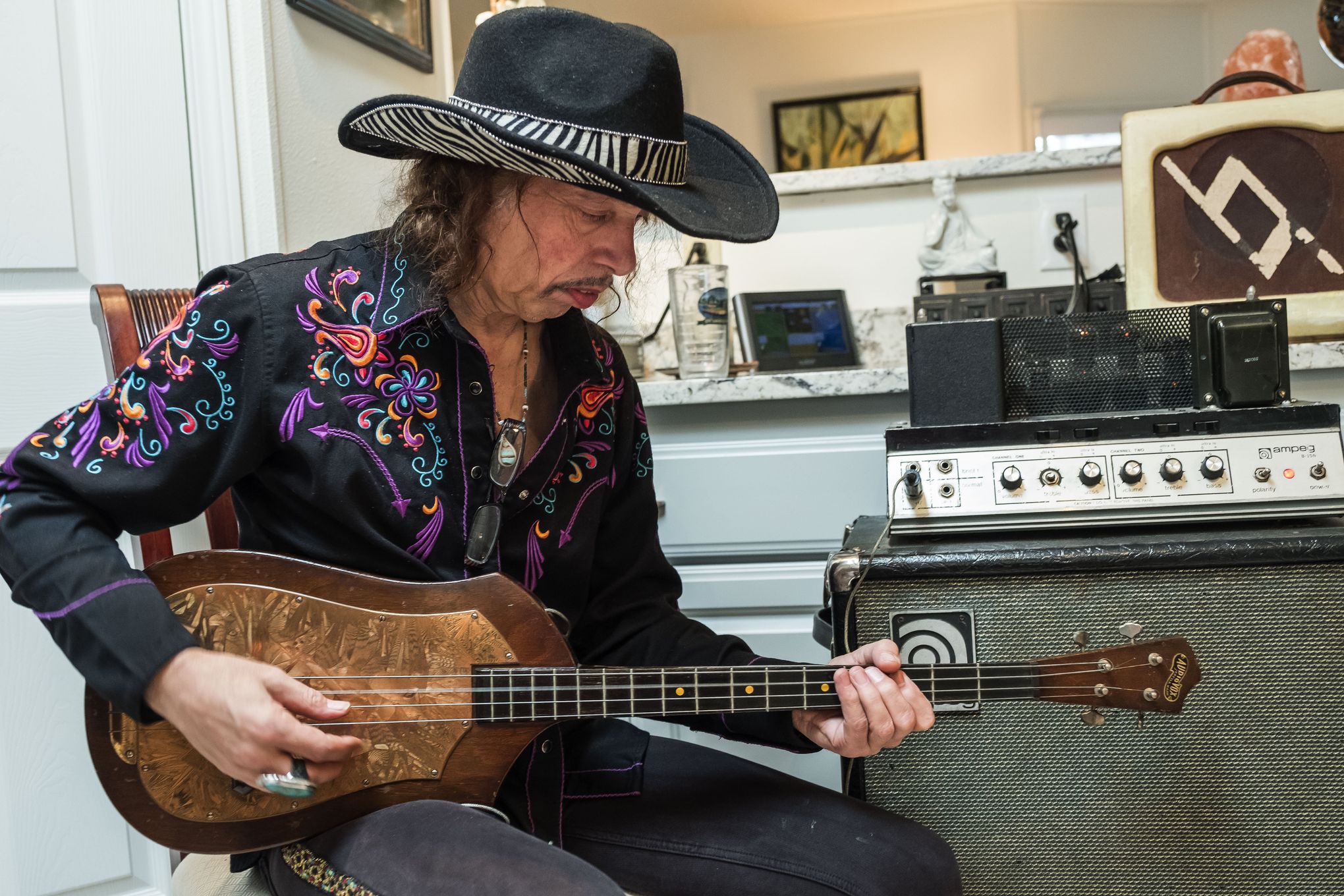
Credit: www.seattletimes.com
Design And Parts Of The Bass Guitar
The Design and Parts of the Bass Guitar play a critical role in shaping its sound and playability. From the pendant-like headstock to the robust body, each component of a bass guitar is crafted to fulfill both functional and aesthetic purposes. A bass guitar appears simple at first glance, but a closer look reveals the intricate design and interplay of its parts that create the deep, resonating tones bassists love.
Overview Of The Main Components
A bass guitar is made up of several key components:
- Headstock: Holds the tuning machines and often displays the guitar’s brand.
- Neck: The long piece of wood that supports the fretboard, tuners, and headstock.
- Fretboard: Often made from rosewood or maple, this is where the frets are housed.
- Body: The large wooden part to which the neck is attached. It houses the pickups and electronics.
- Pickups: Electromagnetic devices that capture the string vibrations and convert them to an electrical signal.
- Bridge: Supports the strings and transmits vibrations to the body of the guitar.
- Tuning machines: Allow players to tune the strings to the correct pitch.
- Control knobs: Adjust volume and tone settings.
Differences In Design Among Various Types Of Bass Guitars
Bass guitars can vary immensely in design:
- Body Shape: Choices range from classic designs to modern, edgy shapes.
- Neck Joint: Options include bolt-on, set-neck, or neck-through constructions, each affecting tone and sustain.
- String Configuration: Four-string models are standard, but five, six, and even eight-string variants exist for wider tonal possibilities.
- Scale Length: This varies from short-scale for a warmer tone to long-scale for more punch and sustain.
- Electronics: Active or passive pickups alongside a range of pre-amps and tone shapers.
Materials Commonly Used In Bass Guitar Construction
The materials used in making a bass guitar affect its sound, weight, and durability:
- Woods: Bodies are often made of ash, alder, or mahogany, while necks can be maple or rosewood.
- Hardware: Typically made of steel or brass for strength and resilience.
- Finish: Polyurethane or nitrocellulose, which protect the wood and enhance its appearance.
- Strings: Usually made of nickel or stainless steel.
Different combinations of materials contribute to the unique sonic characteristics and feel of each bass guitar.
Manufacturing Process Of A Bass Guitar
The manufacturing process of a bass guitar is both an art and a science. From the selection of quality woods to the precision installation of electronics, each step is carried out with meticulous care. Crafting a bass guitar involves a symphony of techniques to ensure the resulting instrument not only looks stunning but also delivers in terms of sound quality and playability. Let’s dive into the fascinating journey of bass guitar creation!
Step-by-step Process Of Crafting The Body
Creating the body of a bass guitar is a process that begins with selecting the right wood. Common choices include maple, alder, and mahogany, each known for its unique sonic properties. The wood is then cut and shaped into the classic contours of a bass guitar body.
- Wood Selection: Choosing the type of wood based on tonal characteristics.
- Cutting: Wood is cut into a rough body shape using templates.
- Routing: Cavities for pickups and electronics are meticulously routed out.
- Sanding: The body is sanded smooth, prepping it for further steps.
The Creation Of The Bass Guitar Neck And Fretboard
Parallel to body crafting, the neck takes shape from sturdy wood like maple or mahogany, ensuring it can withstand years of play. A separate piece of wood is often used for the fretboard—typically rosewood or ebony—where frets are carefully installed. Precise alignment is crucial for optimal playability.
- Neck Shaping: The neck blank is cut and carved to the desired profile.
- Fretboard Application: The fretboard is glued onto the neck.
- Fret Installation: Frets are installed with precision ensuring even spacing.
- Truss Rod Insertion: Truss rod is inserted for neck adjustability and support.
Assembling The Hardware And Electronics
With the body and neck ready, focus shifts to installing hardware and electronics. The bass guitar begins to take functional form with the addition of tuning machines, bridge, pickups, and controls for volume and tone. Electronics installation is a delicate task, requiring expertise to secure optimal sound transmission.
Component | Function | Installation Detail |
---|---|---|
Tuning Machines | For string tension and tuning stability | Attached to the headstock |
Bridge | Supports strings and transfers vibrations | Secured to the body |
Pickups | Captures string vibration and converts to an electrical signal | Mounted onto the body |
Electronics | Volume and tone control | Soldered and fitted within body cavities |
Finishing Touches: Painting And Polishing
The final phase involves painting and polishing the bass guitar to perfection. This can range from simple stains to elaborate custom graphics. Once painted, the guitar is polished to a high gloss or given a matte finish, depending on the desired aesthetic. This step not only gives the guitar its visual appeal but also protects the wood.
- Sealing the Wood: A sealant is applied to protect the wood grain.
- Painting: Several coats of paint are applied with adequate drying time between each.
- Clear Coating: A clear coat is applied for added protection and gloss.
- Polishing: The guitar is polished to a smooth, gleaming finish.
Quality Control And Testing
Behind every resonant pluck of the bass guitar, there’s an intricate process of quality control and testing that ensures every instrument achieves its signature deep tone and durability. This critical phase is where the abstract art of luthiery meets the concrete demands of musicianship, ensuring that every bass guitar not only looks stunning but performs flawlessly on stage and in the studio.
Quality Assurance In Materials And Craftsmanship
The foundation of an exceptional bass guitar starts with selecting premium materials and meticulous craftsmanship. The journey begins in the woodshop where each piece of timber is carefully evaluated. Species such as maple, rosewood, and ash are chosen for their tonal properties and endurance. Here’s what quality assurance entails:
- Grain inspection: to prevent future warping or cracking.
- Moisture content analysis: ensuring the wood is adequately dried for optimal resonance.
- Component precision: scrutinizing the neck and body joinery for a snug fit.
Metal parts, such as tuning machines and pickups, undergo a similar suitability examination. Only the highest-grade hardware makes it onto the instruments.
Sound Testing And Adjustments
With a firm structure in place, sound testing takes center stage. Refined ears assess every nuance from sustain to timbre, ensuring the bass emits a balanced and harmonic-rich tone. Expert technicians work through a detailed checklist:
- Testing string height
- Adjusting pickup response
- Evaluating electronics for consistency
Adjustments are precise, from the truss rod to the intonation settings, guaranteeing playability and comfort.
Final Inspection Before Distribution
Before a bass guitar can make its journey to players worldwide, it undergoes a rigorous final inspection. This ultimate evaluation includes:
Aspect | Checked Feature |
---|---|
Aesthetics | Finish, color, and overall appearance |
Functionality | Hardware and electronics operation |
Playability | Action, fretwork, and neck alignment |
Sound | Tonal clarity and output balance |
Only when every feature meets the set benchmarks of excellence, can the bass guitar be packed and sent off, ready to be played by eager musicians hungry for that deep, mesmerizing groove that only a well-crafted bass can deliver.
Innovations In Bass Guitar Manufacturing
The bass guitar, a mainstay in the rhythm section of bands across genres, has undergone significant transformations since its inception. Visionaries in manufacturing have constantly pushed the boundaries of what’s possible, and modern techniques have revolutionized the instrument both in terms of sound and playability. Exploring the newest trends in bass guitar production reveals a fascinating blend of technology, artistry, and sustainability.
Advancements In Materials And Construction Techniques
In the pursuit of superior tone and durability, manufacturers have embraced innovative materials and construction methods. Bass guitars are leaving conventional woods for alternative materials like carbon fiber and thermally modified tone woods, offering remarkable resilience to changes in environment and novel sound qualities. Let’s look at a few groundbreaking changes:
- Multiscale fretboards – These provide optimal tension across strings, enhancing both comfort and playability.
- CNC routing – Computer numerically controlled machinery allows for precise, intricate body shapes and neck contours.
- 3D printing – This technology is now being utilized for producing bespoke components that are difficult to create via traditional woodcraft.
Custom Bass Guitars And Personalization Options
Customization has become the buzzword in contemporary bass guitar production. Musicians can now shape their instruments to reflect their individuality. Options include:
Custom Feature | Benefits |
---|---|
Personalized Inlays | Turns the fretboard into a unique piece of art |
Choice of Pickups | Tailors the sound to the player’s style |
Custom Finishes | Impacts both looks and sound resonance |
Additionally, neck profiles and hardware options can be personalized, ensuring that every aspect of the instrument is optimized for the musician’s comfort and technique.
Sustainable Practices In Bass Guitar Production
The shift towards sustainability has influenced the way bass guitars are made. Going green isn’t just about the environment; it’s about long-term viability for the instrument-making craft. Initiatives include:
- Using responsibly sourced woods, such as those certified by the Forest Stewardship Council (FSC).
- Implementing recycling programs for strings and hardware.
- Experimenting with eco-friendly finishes that reduce harmful emissions.
Manufacturers who adopt these ethical practices not only contribute to the environment but also appeal to the growing demographic of eco-conscious musicians.

Credit: www.openculture.com
What Are the Key Steps in Making a Bass Guitar That Determine Its Difficulty Level?
When considering making a bass guitar easy, several key steps are essential. Selecting the right materials, understanding neck construction, and choosing appropriate hardware all influence playability. Additionally, precise fret placement and setting the action height contribute significantly to ease of use, ensuring that both beginners and seasoned players can enjoy the instrument.
Frequently Asked Questions For How Is The Bass Guitar Made
How Was The Bass Guitar Developed?
The bass guitar evolved from acoustic basses to meet amplification needs in bands. Leo Fender created the first mass-produced electric bass, the Precision Bass, in 1951, revolutionizing low-end music elements. This design offered easier handling and fretted playing, bolstering its popularity among musicians.
How Is An Electric Bass Guitar Made?
An electric bass guitar is crafted by shaping a wooden body and neck, installing electronics, frets, and pickups, then finishing with paint and hardware.
How Hard Is It To Build A Bass?
Building a bass guitar can be challenging for beginners. It requires woodworking skills, patience, and attention to detail. Advanced players with DIY experience may find it a rewarding project.
What Parts Do You Need To Build A Bass Guitar?
To build a bass guitar, you need a body, neck, fretboard, pickups, tuning machines, bridge, control knobs, strings, and input jack. Each part must be compatible for optimal sound.
Conclusion
Crafting a bass guitar involves precision, skill, and an appreciation for music. Passionate artisans work diligently, selecting quality materials to bring rich sounds to life. As we’ve explored, each step in making a bass guitar is pivotal to its unique tone and playability.
Enthusiasts and professional players alike can appreciate the meticulous process that results in these incredible instruments. Embrace the harmony of wood, wire, and craftsmanship in every note played.
{ “@context”: “https://schema.org”, “@type”: “FAQPage”, “mainEntity”: [ { “@type”: “Question”, “name”: “How was the bass guitar developed?”, “acceptedAnswer”: { “@type”: “Answer”, “text”: “The bass guitar evolved from acoustic basses to meet amplification needs in bands. Leo Fender created the first mass-produced electric bass, the Precision Bass, in 1951, revolutionizing low-end music elements. This design offered easier handling and fretted playing, bolstering its popularity among musicians.” } } , { “@type”: “Question”, “name”: “How is an electric bass guitar made?”, “acceptedAnswer”: { “@type”: “Answer”, “text”: “An electric bass guitar is crafted by shaping a wooden body and neck, installing electronics, frets, and pickups, then finishing with paint and hardware.” } } , { “@type”: “Question”, “name”: “How hard is it to build a bass?”, “acceptedAnswer”: { “@type”: “Answer”, “text”: “Building a bass guitar can be challenging for beginners. It requires woodworking skills, patience, and attention to detail. Advanced players with DIY experience may find it a rewarding project.” } } , { “@type”: “Question”, “name”: “What parts do you need to build a bass guitar?”, “acceptedAnswer”: { “@type”: “Answer”, “text”: “To build a bass guitar, you need a body, neck, fretboard, pickups, tuning machines, bridge, control knobs, strings, and input jack. Each part must be compatible for optimal sound.” } } ] }