Building a classical guitar typically takes around 200 to 300 hours. The process can spread over a few months due to curing and resting periods.
Crafting a classical guitar is an intricate art that combines woodworking skills with an understanding of acoustics. Luthiers meticulously shape and assemble various woods to create an instrument with superior sound quality. The time invested includes designing, selecting materials, cutting, assembling, finishing, and finally setting up the guitar for optimal playability.
Each handcrafted piece reflects the maker’s dedication to quality and the rich tradition of classical guitar construction. This time frame ensures that every detail, from the precision of the fretwork to the balance of the string tension, contributes to the instrument’s excellence and uniqueness. Aspiring guitar creators and music enthusiasts appreciate the careful attention to detail that delivers an exceptional musical companion.
Introduction To Classical Guitar Craftsmanship
The creation of a classical guitar is both an art and a precise science, blending tradition with meticulous handcrafting. The process is steeped in history and requires a level of patience and skill that culminates in the creation of a timeless musical instrument. Crafting a classical guitar is a harmonious dance between the luthier and the materials selected, each bend of wood, each stroke of the planer, and each strum on the strings telling a story of dedication and passion.
Brief History Of Classical Guitar
The classical guitar, with its rich history, traces its roots back to the Renaissance and Baroque eras, evolving over centuries from the earlier instruments like the lute and vihuela. The modern design was revolutionized by Spanish luthier Antonio de Torres in the 19th century, whose techniques and proportions set the standard for what we recognize as the classical guitar today.
Understanding The Elements Of A Classical Guitar
To appreciate the complexity of building a classical guitar, one must first understand its components:
- Top: The soundboard of a guitar, typically made from spruce or cedar, is critical to the instrument’s sound production.
- Back and Sides: Often crafted from hardwoods like rosewood or mahogany, these elements contribute to the guitar’s tone and structural stability.
- Neck: Usually constructed from mahogany or cedar, the neck holds the fretboard and must balance strength with playability.
- Fretboard: Made of harder woods like ebony, it’s where the fingers meet the strings to create notes.
- Bridge: Where the strings are anchored to the soundboard, playing a pivotal role in tone and resonance.
Each part, crafted and assembled with precision, affects the playability, sound quality, and aesthetic appeal of the finished instrument. The meticulous selection of these materials reflects the luthier’s expertise and the guitar’s potential for excellence.

Credit: www.texasmonthly.com
The Guitar Maker’s Journey: From Wood Selection To Stringing
The journey of a guitar maker is a symphony of precision, craftsmanship, and patience. Creating a classical guitar is not merely an act of assembly but an artistic endeavor that blends tradition and technical skill. From the moment the woods are selected to the final stringing, every step is pivotal in shaping the instrument’s character and voice. Hours turn into days, and days may stretch into months, as luthiers meticulously transform simple materials into an intricate and resonant work of art.
Selecting The Right Tonewoods
The foundation of a guitar’s tone comes from its tonewoods. A guitar maker must possess both knowledge and intuition when choosing the woods that will define their instrument’s voice. Different species offer unique sounds and aesthetics:
- Spruce for a bright, articulate soundboard
- Rosewood for deep resonances in the back and sides
- Mahogany for warmth and balance throughout
A perfect selection ensures not only beauty but also the ideal acoustic properties desired in a classical guitar.
Shaping The Guitar Body And Neck
The transformation of wood slabs into a guitar’s body and neck is a testament to the luthier’s skill. Each curve and contour is carved with precision. The body’s shape affects sound projection and playability, while the neck’s design is crucial for the guitarist’s comfort. Accuracy in this stage is vital for the instrument’s overall balance and performance.
Bracing And Soundboard Construction
Bracing patterns within a guitar have an enormous impact on sound characteristics. The construction of the soundboard, coupled with the strategic placement of braces, determines the instrument’s resonance and strength. Luthiers use time-honored techniques to delicately shape and position these internal supports, crafting a soundboard that dances with the music.
The Intricacies Of The Fingerboard And Frets
Upon a closer look, the complexity of the fingerboard and frets reveals itself. The choice of hardwoods for the fingerboard like ebony ensures durability and a sleek playing surface. Installing frets requires accuracy down to the millimeter—any deviation can impact intonation and playability. A luthier’s expertise is clear in the smooth action and precise intonation of the finished fretwork.
Timeframe For Constructing A Classical Guitar
The creation of a classical guitar is a blend of art and craftsmanship that beckons the question: Just how long does this intricate process take? Understanding the timeframe is crucial for both budding luthiers and seasoned guitar enthusiasts alike. It’s a journey laden with precision and passion, and the time investment varies depending on numerous factors.
A Step-by-step Breakdown Of The Building Process
The construction of a classical guitar can be divided into several key steps. While this is a simplified overview, each stage involves detailed work that contributes to the overall timeframe.
- Selecting the Wood: Choosing quality tonewoods that will influence the sound and durability of the instrument.
- Molding and Shaping: Shaping the wood for the guitar’s body, neck, and other components.
- Assembling the Body: Joining the top, back, and sides of the guitar, often involving delicate gluing and clamping.
- Neck Attachment: Precisely aligning and securing the neck to the body.
- Fretwork: Installing the frets and ensuring proper intonation.
- Finishing: Applying varnish or lacquer, and allowing time for it to cure.
- Final Assembly: Attaching the bridge, tuning machines, and strings.
- Setup: Adjustments made to action, intonation, and final playability tests.
Factors Affecting The Construction Timeline
Several factors heavily influence the duration of building a classical guitar:
- Experience Level: Skilled luthiers work faster than novices due to refined techniques.
- Complexity of Design: Custom inlays and intricate details add to the timeline.
- Tools and Equipment: Access to high-quality tools can expedite certain steps.
- Drying and Curing Times: Climate and humidity impact the time required for wood and finishes to settle.
- Availability: Full-time builders can allocate more daily hours compared to hobbyists.
Average Duration For Amateur Luthiers Vs. Professionals
Amateur luthiers may take several months to over a year to build a classical guitar, as they’re often balancing the project with other commitments and are still mastering their craft. In contrast, professional luthiers may complete a guitar in one to three months, leveraging their expertise and efficiency to minimize the timeline while maintaining impeccable quality.
Below is an estimated comparison:
Builder Type | Estimated Timeframe |
---|---|
Amateur Luthier | 6-18 months |
Professional Luthier | 1-3 months |
This overview gives aspiring makers and guitar lovers insights into the dedication and patience required to craft a classical guitar. Patience, above all, is essential, as each handcrafted instrument can be seen as a personal labor of love, with its own unique timeline.
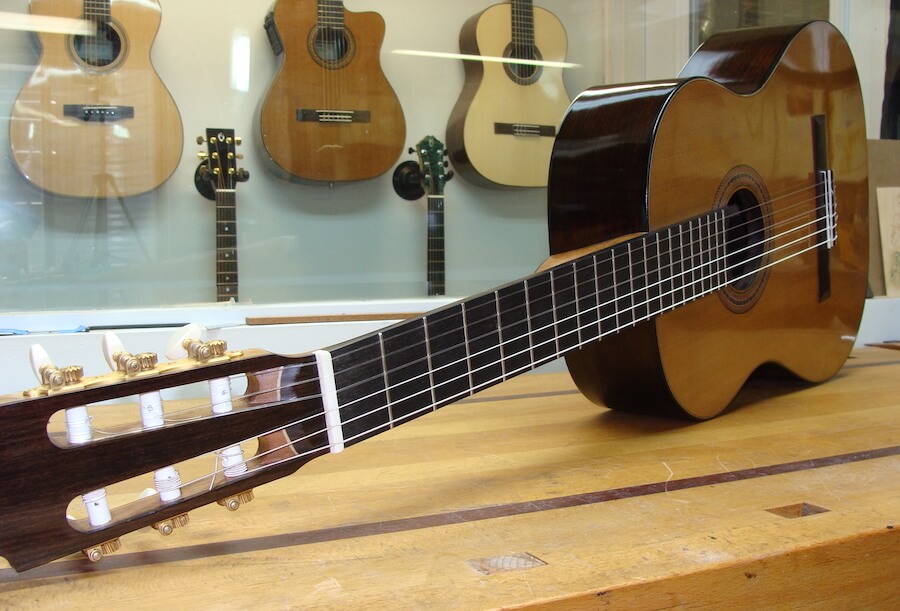
Credit: lutherieacademy.com
Finishing Touches And Quality Control
The journey of crafting a classical guitar reaches its most intricate point during the finishing touches and quality control phase. This is the moment where the instrument not only gains its final aesthetic appeal but also undergoes rigorous checks to ensure that the sound it produces matches the high standards set by master luthiers. Precision and patience are paramount as we dive into the final stages of creating a musical masterpiece.
Applying The Finish And Curing Time
Applying the finish is a critical step in guitar construction. It protects the wood from environmental damage and enhances the guitar’s visual appeal. Various finishes can be applied, from French polish to nitrocellulose lacquer, depending on the desired look and sound impact. The process involves:
- Preparing the surface: sanding the guitar to a smooth finish is crucial for an even application.
- Applying the finish: multiple thin coats are applied, with sufficient drying time in between.
- Final touching: achieving a perfect finish may include sanding between coats and even a final buffing once all layers are cured.
Curing time can vary substantially, ranging from a few days to several weeks, depending on the type of finish and atmospheric conditions. The curing process is essential as it solidifies the finish, making it durable and enhancing the acoustics of the guitar.
Final Assembly And Setup
Once the finish is fully cured, the guitar moves to final assembly and setup. This delicate stage involves:
- Securely attaching the neck to the body, if not already done.
- Installing the tuning machines, ensuring they are aligned and work smoothly.
- Fitting the bridge and nut, which play a vital role in intonation and action.
- Stringing the guitar and precisely adjusting the action and intonation for optimal playability.
A well-set-up guitar feels comfortable to play and responds well to the musician’s touch.
Quality Assurance And Sound Testing
The final and perhaps most important step is quality assurance and sound testing. Each classical guitar undergoes a thorough inspection process, which includes checking:
- Structural integrity: ensuring no cracks, loose joints, or stability issues.
- Workmanship: confirming all aesthetic elements meet quality standards, including inlays and binding.
- Playability: evaluating the action height, fret work, and overall comfort.
- Sound: every note is played to test for tonal consistency, sustain, and clarity. Expert ears listen for the guitar’s resonance, balance, and volume across all strings and frets.
Only after passing these meticulous tests does a classical guitar earn the right to be played by the hands of a musician, promising an exquisite musical experience.
The Impact Of Craftsmanship On Playability And Sound
The craftsmanship behind a classical guitar plays a pivotal role in its playability and sound quality. Meticulous attention to detail and the use of high-quality materials define the soul of the instrument, shaping the nuances of its voice. Every curve, string action, and choice of wood contributes to the tactile and auditory experience of the musician.
The Relationship Between Time Invested And Instrument Quality
Dedication to the art of guitar making is reflected in the subtleties of sound and playability. Skilled luthiers understand that each step of the process, from wood selection to final polish, significantly affects the end result:
- Careful wood curing and selection ensure stability and resonance.
- Precision in bracing patterns contributes to the instrument’s tonal character.
- Fine-tuning the neck angle enhances the guitar’s action and player comfort.
Adequate time investment in these areas is crucial. High-quality classical guitars often necessitate hundreds of hours to complete, signifying a direct relationship between the time invested and the excellence of the instrument.
Case Studies: Notable Luthiers And Their Timelines
Several iconic luthiers have set standards in the guitar-building community. Their timelines vary based on technique, experience, and design complexity:
Luthier | Build Time | Signature Approach |
---|---|---|
Antonio Torres | 1-2 months | Innovative fan bracing |
Hermann Hauser | 3-4 months | Refinement of Torres’ methods |
Robert Bouchet | 4-6 months | Artistic and technical precision |
These timelines exhibit the diversity among craftsmen and the individualized nature of guitar building.
Care And Maintenance Post-build To Preserve Sound Quality
After a classical guitar is built, consistent care is integral to maintain its sound quality. Essential maintenance includes:
- Regular cleaning and polishing to protect the wood and finish.
- String replacement to sustain tone and intonation.
- Monitoring humidity and temperature to prevent wood damage.
Owners should approach care with the same meticulousness as the luthier who built the guitar to ensure longevity and performance.
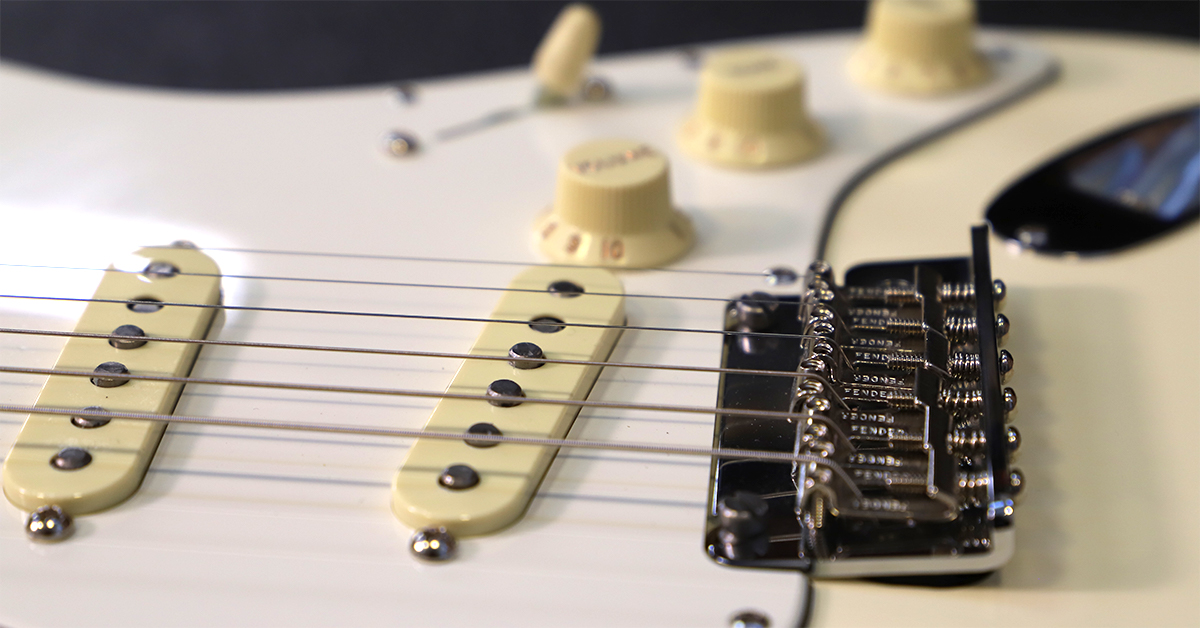
Credit: www.sweetwater.com
How Does the Time Required to Build a Classical Guitar Vary Depending on the Materials and Tools Used?
The time required to build a classical guitar largely depends on the essential materials for building a classical guitar. High-quality woods, specialized tools, and adhesives can streamline the process, while less suitable options may prolong it. Choosing the right combination is crucial for both efficiency and the final sound quality of the instrument.
Frequently Asked Questions Of How Long Does It Take To Build A Classical Guitar
How Fast Can You Build A Guitar?
Building a guitar can vary in time, typically taking several weeks to months. Expert luthiers may complete custom builds faster, around 200 hours of work, depending on complexity and design.
How Long Does The Guitar Building Process Take?
Building a guitar typically takes between 200 to 300 hours. The time can vary based on the builder’s expertise and the instrument’s complexity.
How Long Does It Take To Build A Martin Guitar?
Building a Martin guitar typically takes about three to four months, depending on the model and customization.
How Long Will It Take To Master Classical Guitar?
Mastering classical guitar typically takes several years. Beginners may need five years, while advanced proficiency can require a decade or more of dedicated practice.
Conclusion
Crafting a classical guitar is a blend of artistry and patience. The process often spans months, depending on a number of variables. From wood selection to the final polish, each step infuses character, ensuring no two instruments are identical. Embrace the journey if you’re considering this endeavor; the final chord will reflect your dedication and skill.
{ “@context”: “https://schema.org”, “@type”: “FAQPage”, “mainEntity”: [ { “@type”: “Question”, “name”: “How fast can you build a guitar?”, “acceptedAnswer”: { “@type”: “Answer”, “text”: “Building a guitar can vary in time, typically taking several weeks to months. Expert luthiers may complete custom builds faster, around 200 hours of work, depending on complexity and design.” } } , { “@type”: “Question”, “name”: “How long does the guitar building process take?”, “acceptedAnswer”: { “@type”: “Answer”, “text”: “Building a guitar typically takes between 200 to 300 hours. The time can vary based on the builder’s expertise and the instrument’s complexity.” } } , { “@type”: “Question”, “name”: “How long does it take to build a Martin guitar?”, “acceptedAnswer”: { “@type”: “Answer”, “text”: “Building a Martin guitar typically takes about three to four months, depending on the model and customization.” } } , { “@type”: “Question”, “name”: “How long will it take to master classical guitar?”, “acceptedAnswer”: { “@type”: “Answer”, “text”: “Mastering classical guitar typically takes several years. Beginners may need five years, while advanced proficiency can require a decade or more of dedicated practice.” } } ] }