Electric guitars typically feature bodies made of wood and necks also crafted from wood. The strings are usually made of steel or nickel.
Electric guitars have sparked revolutions in the music world, blending craftsmanship with technology to produce a wide range of sounds. Essential to genres like rock, jazz, and blues, these instruments owe their distinctive tones to their construction materials. The choice of wood, for example, from maple to mahogany, significantly influences the guitar’s sound and playability.
Key components like the pickups, which convert string vibrations into electrical signals, are often made from magnets and coils of wire. Together with the guitar’s hardware, including tuners and bridges made of metals like chrome or nickel, these materials create the dynamic soundscapes artists and listeners adore. Electric guitar designs balance aesthetics and sound quality, ensuring that these instruments look as good as they play.

Credit: www.quora.com
Introduction To Electric Guitars
Electric guitars resonate with the soul of modern music. These iconic instruments transform vibrations into electrical signals, creating a spectrum of sounds that have shaped multiple genres and inspired millions. With the versatility to produce gentle rhythms or searing solos, electric guitars remain at the core of musical innovation and cultural expression.
The Evolution Of The Electric Guitar
The journey of the electric guitar began in the early 20th century, with experimentations aimed at amplifying the sound of traditional acoustic guitars. Inventors sought to capture the guitar’s essence and power it through speakers, leading to the creation of the first electrically amplified guitars. Rickenbacker, Fender, and Gibson are among the legendary names that pioneered designs and technologies, each contributing to the electric guitar’s evolution.
Electric Guitars In Modern Music
From rock ‘n’ roll to jazz, from blues to metal, electric guitars have been at the forefront of music for decades. Their ability to produce a wide range of tones makes them essential for contemporary musicians. Electrifying riffs and melodic lines executed on electric guitars have defined the soundtracks of generations and continue to influence modern musical landscapes.
Basic Components Of Electric Guitars
- Body: Typically crafted from woods such as alder, maple, or mahogany, the body affects the guitar’s tone and sustain.
- Neck: The neck, which can be made of similar woods as the body, supports the fretboard and is a crucial element for playability.
- Fretboard: Often made from rosewood or ebony, the fretboard contains the frets and influences both the feel and the tone of the instrument.
- Pickups: These magnetic components detect string vibrations and convert them into an electrical signal for amplification.
- Controls: Volume and tone knobs, along with pickup selector switches, enable players to adjust the sound output.
- Bridge: The bridge anchors the strings and can vary in design, impacting the guitar’s intonation and sustain.
Materials Used In Electric Guitar Construction
Musicians and enthusiasts often marvel at the melodic prowess of electric guitars, but the materials that comprise these iconic instruments are equally fascinating. Each material contributes to the unique sonic fingerprint and aesthetics of a guitar. Let’s delve into the various substances that are meticulously crafted to bring electric guitars to life.
Types Of Wood For Guitar Bodies
The body of an electric guitar serves as the foundation for its tone and resonance. Typically, guitar makers choose woods based on their ability to balance weight, durability, and sound quality.
- Alder: Known for its light weight and balanced tone, alder is a popular choice for many mainstream guitar models.
- Mahogany: Favored for its rich, warm tones, mahogany provides excellent sustain and depth.
- Ash: With its bright, twangy sound and attractive grain patterns, ash is often seen in vintage-style guitars.
Neck And Fretboard Woods
The neck and fretboard significantly affect playability and fingerboard resonance. Various woods are selected to enhance these characteristics.
Wood Type | Tonal Qualities |
---|---|
Maple | Bright and snappy, ideal for clear, sharp notes |
Rosewood | Warm and rich, preferred for its smooth feel |
Wenge | Dense and durable, with a distinctive tone and texture |
Metal Components: Pickups, Bridges, And Tuners
Metal parts are crucial to function and sustain. The selections made here are critical to the instrument’s overall sound and stability.
- Pickups:
- Usually made of magnets wrapped with wire, they convert string vibrations into electrical signals.
- Bridges:
- Metal bridges anchor the strings and adjust their spacing and height for proper intonation.
- Tuners:
- Precision metal tuners maintain string tension and pitch accuracy.
Synthetic Materials: Nuts And Pickguards
Beyond natural woods and metals, electric guitars also make use of synthetic materials for certain components.
- Nuts: Often crafted from plastics like Tusq or Corian, nuts establish the strings’ spacing at the headstock.
- Pickguards: Made from various plastics, pickguards protect the guitar’s finish and add a visual flair.
Electronic Components: Wiring And Potentiometers
The heart of an electric guitar’s functionality lies within its electronics. Effective wiring ensures signal clarity, while potentiometers control volume and tone.
- Wiring: Quality copper wire connections between components minimize noise and interference.
- Potentiometers: These variable resistors are essential for tailoring the guitar’s sound to a player’s preference.
Manufacturing Process Of Electric Guitars
The manufacturing process of electric guitars is a blend of art and engineering, a symphony where precision meets passion. The creation of these beloved instruments involves various steps, each crafted to ensure not only impeccable sound quality but also a visually stunning piece of craftsmanship. From choosing the right materials to the final setup, we will dive into the intricacies of what goes into building an electric guitar under the spotlight of the workshop.
Designing And Selecting Materials
- Design Specifications: CAD (Computer-Aided Design) tools or hand-drawn schematics to flesh out the exact dimensions and aesthetics.
- Wood Selection: Choice oftentimes includes maple, mahogany, alder, and ash for their tonal properties and durability.
- Hardware and Electronics: Manufacturers choose pickups, tuners, bridges, and other components based on desired sound and functionality.
Shaping The Body And Neck
CNC machines or hand-crafted techniques are employed to:
- Cut the chosen wood into the classic contours of the guitar body.
- Carve the neck and headstock, integral for player comfort and string stability.
- Craft the fretboard, where skilled workers install the frets and position inlays with precision.
Electronics Installation And Testing
Electric guitars come alive in this phase as:
- Pickups are installed—these magnetic components capture string vibrations and convert them into electrical signals.
- Wiring the pots (potentiometers) and switches under the pickguard or within the body cavities that will control volume and tone.
- Testing for electronic functionality to ensure each component is operative.
Finishing: Painting And Varnishing
The visual appeal of the guitar takes shape with:
Process | Description |
---|---|
Sanding | Smoothens the guitar surface in preparation for painting. |
Painting | Several coats applied for a deep, rich color. |
Varnishing | Protective layers to seal the paint and enhance gloss. |
Quality Control And Final Assembly
Before the guitar reaches a musician’s hands:
- Inspection: Expert eyes scrutinize every detail for flaws or imperfections.
- Setup: Neck attachment, stringing, and precise adjustment of the bridge and truss rod for optimal playability.
- Play-testing: Experienced guitarists test the feel and sound, ensuring the instrument meets the brand’s quality standards.
From the initial design to the final note, the journey of manufacturing an electric guitar is calibrated for quality and performance. With each phase meticulously executed, the end result is an instrument ready to make music history.
Influence Of Materials On Sound And Playability
Every electric guitar tells a story, not only through its design and craftsmanship but also through the unique combination of materials used in its construction. These elements are intricately linked to the distinctive sound and playability of the instrument. Musicians often seek a perfect blend of tonal quality and ease of handling, and finding the right mix can truly elevate their performance. This exploration of materials dives into how various components contribute to an electric guitar’s character and responsiveness, paving the way for a rich and personal playing experience.
The Impact Of Wood Types On Tone
The type of wood used in an electric guitar does much more than just define its outer appeal. Different woods have distinctive properties that can profoundly influence the tonal characteristics of the instrument. For instance, a guitar made from mahogany yields a warm, rich sound with excellent sustain, while maple is known for its bright, clear tone and good projection. Understanding how wood types affect sound is essential for any musician seeking a certain audio signature.
- Mahogany: Delivers a warm, rich and full-bodied tone, with great sustain.
- Maple: Known for its bright, clear, and well-projected sound, often with a sharp attack.
- Ash: Offers a balanced tone with excellent sustain and a punchy, snappy quality.
- Alder: Popular for its light weight and a full-bodied sound with rich midrange.
How Electronics Shape Guitar Sound
Beyond the wood, an electric guitar’s personality comes to life through its electronic components. Pickups, potentiometers, and capacitors work in unison to capture and shape the guitar’s voice. For example, single-coil pickups generally produce a crisp, articulate tone, whilst humbuckers offer a more powerful, noise-free signal. The configuration and quality of these components are key to the versatility and specificity of a guitar’s sound.
Component | Characteristic Impact |
---|---|
Pickups | Define the primary tonal quality, from bright and twangy to rich and warm. |
Potentiometers | Control the volume and tone, affecting the sound’s brightness and clarity. |
Capacitors | Work with potentiometers to shape the high-frequency response. |
The Role Of Construction In Playability
The way an electric guitar is built influences how it feels in the hands of a musician. From the neck’s profile and scale length to the fretboard’s radius and the action of the strings, construction is a determinant of playability. Guitars with a thin neck profile and low action are typically easier on the fingers, allowing for speedy play and comfortable transitions. The build quality also plays into the instrument’s durability, which is a concern for touring musicians who demand reliability night after night.
Customization And Upgrades
Personalizing an electric guitar by swapping out hardware or electronics allows musicians to fine-tune their sound and playability even further. Upgrades can include installing higher-quality tuners for better tuning stability, changing to a different type of bridge for enhanced sustain, or experimenting with various pickup types to explore new tonal realms. These modifications empower players to mold their instruments into something that is truly their own, reflecting their unique style and preferences.
Common upgrades include:
- High-precision tuners for improved tuning stability.
- Custom pickups to alter the tonal character.
- Replacement bridges for better sustain and intonation.
- Upgraded electronics for more tonal versatility.
Maintaining And Caring For Electric Guitars
Electric guitars, with their mesmerizing sound and unique appeal, require consistent maintenance to ensure they perform at their best. Caring for these instruments encompasses a broad range of tasks, from simple surface cleaning to complex electronic troubleshooting. Leverage these essential guidelines to keep your guitar in pristine condition and sounding excellent.
Cleaning And Condition Of Guitar Surfaces
First impressions matter, and for electric guitars, the allure starts with a clean and well-conditioned surface. Begin by wiping down the body and neck with a soft, lint-free cloth to remove fingerprints and dust. For deeper cleaning, use a specialized guitar polish formulated for your guitar’s finish.
- Fretboards deserve extra attention, especially those made of porous woods like rosewood or ebony. Use a mild cleaner and a conditioning oil to protect the wood and prevent dryness.
- For strings, a simple wipe down after playing will suffice, but consider using a string cleaner for longevity and better playability.
Regular Maintenance Of Hardware
The longevity of your guitar also depends on the integrity of its hardware. Regularly check components like tuning machines, bridges, and strap locks for looseness or wear. Tighten screws and bolts with appropriate tools, ensuring not to over-tighten, which could damage the wood or hardware.
Hardware Component | Maintenance Check | Frequency |
---|---|---|
Tuning Machines | Lubricate gears, tighten tuning keys | Annually or as needed |
Bridge | Clean saddles, check intonation | Every string change |
Strap Locks | Inspect for wear, tighten bolt | Quarterly |
Electronics Care And Troubleshooting
Electric guitars are as much about electronics as they are about wood and strings. Regular cleaning of potentiometers (knobs) and switch contacts can prevent scratchy sounds or signal loss. Using contact cleaner can resolve these issues without harming the electronic components.
- Disconnect the guitar from any power source.
- Apply contact cleaner to the base of the knobs and switches.
- Rotate the knobs and toggle switches to distribute the cleaner.
- Check for loose connections or solders, and address them promptly.
Professional Setup And Adjustments
Even with meticulous care, professional setup and adjustments are crucial for optimal performance. A skilled technician will address neck relief, string action, and intonation. These setups ensure the guitar plays well, stays in tune, and minimizes fret buzz. Schedule a professional setup:
- Annually:
- For regular players
- Bi-Annually:
- If subject to varying climates or heavy use
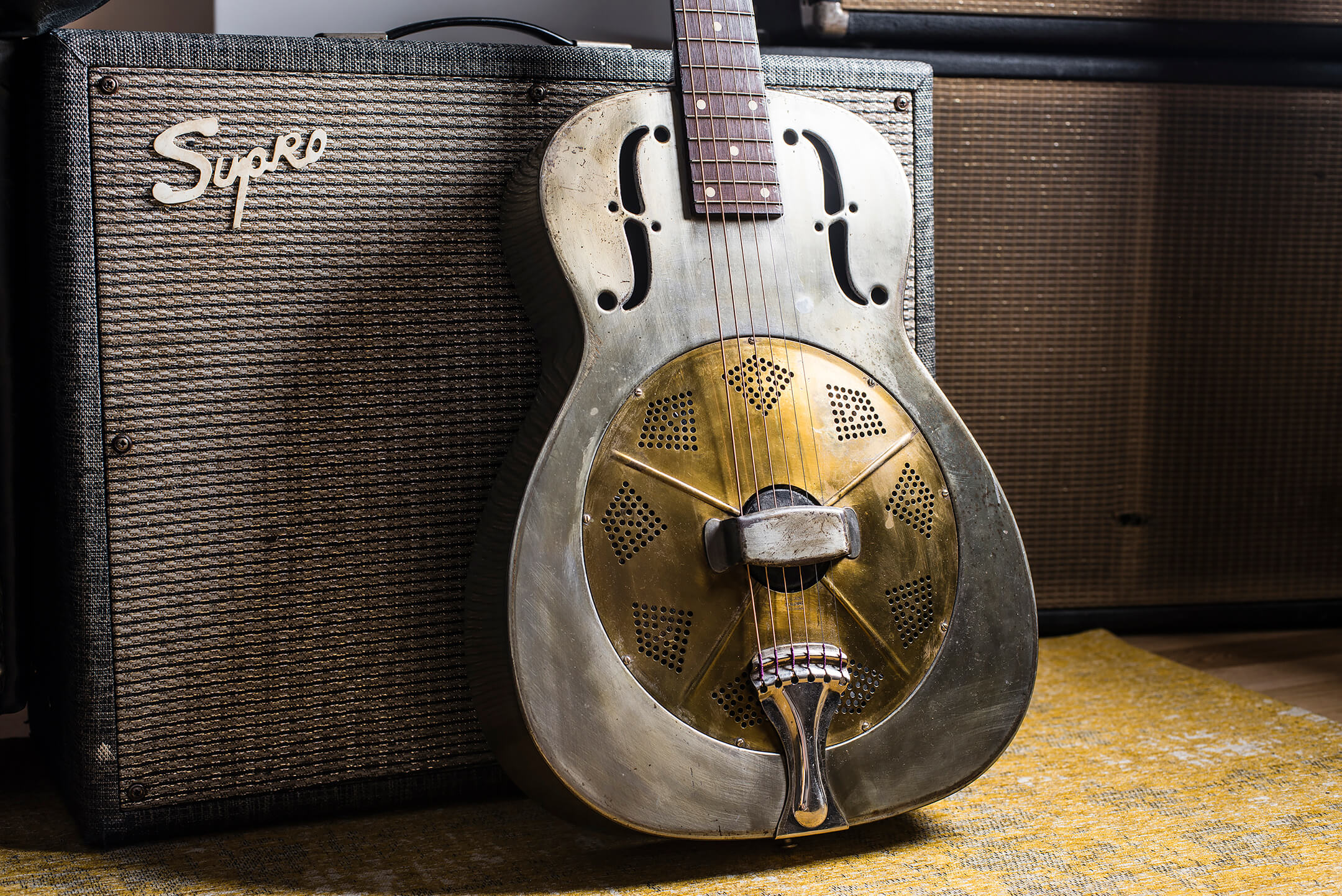
Credit: guitar.com

Credit: en.wikipedia.org
What Materials Are Commonly Used to Make Electric Guitars?
When exploring electric guitars, understanding the basics of electric guitars today can enhance your appreciation. Common materials include solid woods like alder and mahogany for the body, maple for necks, and rosewood or maple for fingerboards. Each material contributes to the guitar’s unique sound and playability.
Frequently Asked Questions Of What Are Electric Guitars Made Of
What Material Is Electric Guitar Made Of?
Electric guitars are typically made of hardwoods like maple or mahogany, with fingerboards of rosewood or ebony. Some models feature bodies made from alternative materials such as acrylic or aluminum for unique tonal properties.
Are Electric Guitars Solid Wood?
Electric guitars often use solid wood, particularly in the body, to enhance sound quality and durability. Some models may incorporate other materials or wood types for specific tonal characteristics.
What Is The Best Electric Guitar Material?
The best electric guitar material often depends on the desired sound and playability. Common top choices include mahogany for warm tones, maple for brightness, and alder for balanced sound profiles.
Does Electric Guitar Wood Really Matter?
Yes, the wood of an electric guitar impacts its tone, resonance, and overall sound quality. Different woods contribute unique characteristics, affecting the instrument’s sonic signature.
Conclusion
Wrapping up, we’ve explored the core materials crafting electric guitars. Wood types, metal components, and synthetic elements all play vital roles. These materials shape not just aesthetics, but also the signature sounds we adore. Remember, your choice reflects your unique sound identity.
Choose wisely and rock on!
{ “@context”: “https://schema.org”, “@type”: “FAQPage”, “mainEntity”: [ { “@type”: “Question”, “name”: “What material is electric guitar made of?”, “acceptedAnswer”: { “@type”: “Answer”, “text”: “Electric guitars are typically made of hardwoods like maple or mahogany, with fingerboards of rosewood or ebony. Some models feature bodies made from alternative materials such as acrylic or aluminum for unique tonal properties.” } } , { “@type”: “Question”, “name”: “Are electric guitars solid wood?”, “acceptedAnswer”: { “@type”: “Answer”, “text”: “Electric guitars often use solid wood, particularly in the body, to enhance sound quality and durability. Some models may incorporate other materials or wood types for specific tonal characteristics.” } } , { “@type”: “Question”, “name”: “What is the best electric guitar material?”, “acceptedAnswer”: { “@type”: “Answer”, “text”: “The best electric guitar material often depends on the desired sound and playability. Common top choices include mahogany for warm tones, maple for brightness, and alder for balanced sound profiles.” } } , { “@type”: “Question”, “name”: “Does electric guitar wood really matter?”, “acceptedAnswer”: { “@type”: “Answer”, “text”: “Yes, the wood of an electric guitar impacts its tone, resonance, and overall sound quality. Different woods contribute unique characteristics, affecting the instrument’s sonic signature.” } } ] }