To build an electric guitar, you need woodworking tools, electronic components, and finishing supplies. Some key tools include a saw, soldering iron, router, and sandpaper.
Building an electric guitar combines the precision of woodworking with the finesse of electronics. It’s a project that captivates the hands-on enthusiast, blending creativity with technical skill. An aspiring luthier starts with woodworking equipment such as saws for cutting the wood to shape and routers for creating cavities.
Sandpaper helps in achieving a smooth surface. The electronic aspect demands a soldering iron for connecting pickups, potentiometers, and input jacks. Finishing supplies could include varnish or lacquer to protect and enhance the guitar’s appearance. Personal protective gear is also essential to ensure safety while crafting this instrument. This fusion of tools and materials transforms raw components into a music-making masterpiece, reflecting its creator’s craftsmanship and artistic vision.
Introduction To Electric Guitar Crafting
Welcome to the fascinating world of electric guitar crafting! For musicians and woodworking enthusiasts alike, the process of building an electric guitar from scratch is an exhilarating journey. It involves precision, creativity, and a deep understanding of the instrument’s mechanics. This introduction to electric guitar crafting is the first step toward creating a unique instrument that resonates with your personal style and sonic preferences.
The Art Of Luthiery: Building Electric Guitars
The craft of building guitars, known as luthiery, is an ancient tradition that has evolved into a modern art form with the introduction of electric guitars. Electric guitar crafting is a meticulous process that requires skill, patience, and a passion for detail. Mastering the art of luthiery unfolds a world of possibilities in design, sound, and playability, making each handmade guitar a one-of-a-kind masterpiece.
Understanding The Basic Components Of An Electric Guitar
To begin crafting an electric guitar, familiarize yourself with its fundamental components. An electric guitar typically consists of:
- Body: The core part that shapes the guitar’s sound and aesthetics.
- Neck: The long piece extending from the body, holding the fretboard.
- Fretboard: Also known as the fingerboard, it contains frets for note differentiation.
- Headstock: Located at the end of the neck, holds the tuning machines.
- Pickups: Magnetic devices that capture string vibrations and convert them into electrical signals.
- Bridge: Supports the strings and transfers vibrations to the body.
- Controls: Include volume and tone knobs, plus a switch to select pickups.
- Hardware: Consists of tuning machines, strap buttons, and output jack.
Each component plays a critical role in the guitar’s functionality and contributes to the overall sound it produces.
Setting Up Your Workspace For Guitar Building
Creating the ideal environment for guitar building is essential for a successful project. Here is a checklist to set up your workspace:
Workspace Requirement | Description |
---|---|
Ample Space | Ensure enough room for tools, components, and maneuverability. |
Proper Lighting | LED or fluorescent lights provide consistent, clear visibility. |
Workbench | A sturdy bench, ideally with a non-slip surface, for detailed work. |
Storage | Organized shelves or drawers for tools and components. |
Ventilation | An exhaust system or open windows to handle dust and fumes. |
Safety Equipment | Gloves, goggles, and hearing protection are non-negotiable. |
Your workspace should promote efficiency, inspire creativity, and most importantly, ensure safety as you bring your electric guitar to life.
Essential Woodworking Tools For Guitar Construction
Creating your own electric guitar combines the harmony of music with the satisfaction of craftsmanship. Essential woodworking tools transform simple pieces of wood into a melodic masterpiece. Each tool plays a crucial role in shaping, securing, drilling, and refining your guitar to perfection. Knowing what you need before you start can save you time, effort, and help you achieve that professional finish.
Choosing The Right Types Of Wood For Your Guitar
Success begins with the foundation – selecting the ideal types of wood for your instrument is critical. Dense hardwoods like mahogany, maple, and ash provide excellent resonance and sustain. For fretboards, rosewood and ebony are popular choices. Consider woods that not only sound good but also appeal to your aesthetic preferences.
Saws, Planes, And Chisels: Shaping The Guitar Body
- Band Saw – Critical for cutting out the rough shape of the body.
- Hand Planes – Essential for flattening surfaces and trueing edges.
- Chisels – Used for the intricate handwork and fine adjustments.
Mastery over these tools ensures the guitar’s body is crafted with precision and care.
Clamps And Vices: Securing Pieces During Assembly
Assembly demands stability. A selection of bar clamps, C-clamps, and vices is indispensable. They hold components firmly as glue sets, preventing any unwanted movement that could compromise the structure.
Drills And Bits: Precision Holes For Hardware Installation
Drill presses and hand drills, complemented by an assortment of bits, are necessary for installing tuners, bridge, and strap buttons. These tools offer the exactness required for flawless functionality.
Sanding Tools: Achieving A Smooth Finish
A smooth finish is not only aesthetically pleasing but also influences the playability of the guitar. Utilize a mix of sanding blocks, orbital sanders, and sanding papers of various grits to refine every surface and edge to perfection.
Router: Creating Cavities For Electronic Components
The router, a pivotal tool, carves out precise cavities for pickups, electronics, and the neck joint. Mastery over the router is essential for a seamless integration of electronic components.
Electronics And Hardware Installation Tools
Constructing an electric guitar is an intricate process that requires precision and care, especially when installing electronics and hardware. A number of specialized tools are essential for creating a well-functioning instrument. This section details the tools crucial for soldering, testing and troubleshooting circuits, preparing wiring, and securing hardware—all vital for the perfect electric guitar.
Soldering Iron: Establishing Electrical Connections
Soldering irons are indispensable when it comes to connecting the electronic components within your guitar. A reliable soldering iron with adjustable temperature settings allows you to create strong, conductive joints between wires, pickups, and potentiometers.
Digital Multimeter: Testing And Troubleshooting Circuits
Using a digital multimeter is key for ensuring your guitar’s electronics are functioning correctly. It helps you measure voltage, current, and resistance within the circuit, assisting in identifying any faulty connections or components before your guitar is fully assembled.
Wire Cutters And Strippers: Preparing Wiring
Wire cutters and strippers help in cutting to length and removing insulation from wires, preparing them for soldering. Precision tools will ensure clean cuts and prevent damage to the wire’s core, which could affect signal quality.
Screwdrivers And Wrenches: Securing Hardware
A set of screwdrivers and wrenches is essential for assembling and securing the various hardware components like tuners, bridge, and strap buttons on your electric guitar. These tools provide the leverage needed to tighten and align parts with control and accuracy.
Shielding Materials: Minimizing Electrical Noise
To preserve the clarity of your guitar’s sound, shielding materials are used to minimize electrical noise. Conductive paints, copper tape, or foil lined in the cavity of the guitar can provide an essential barrier against interference.
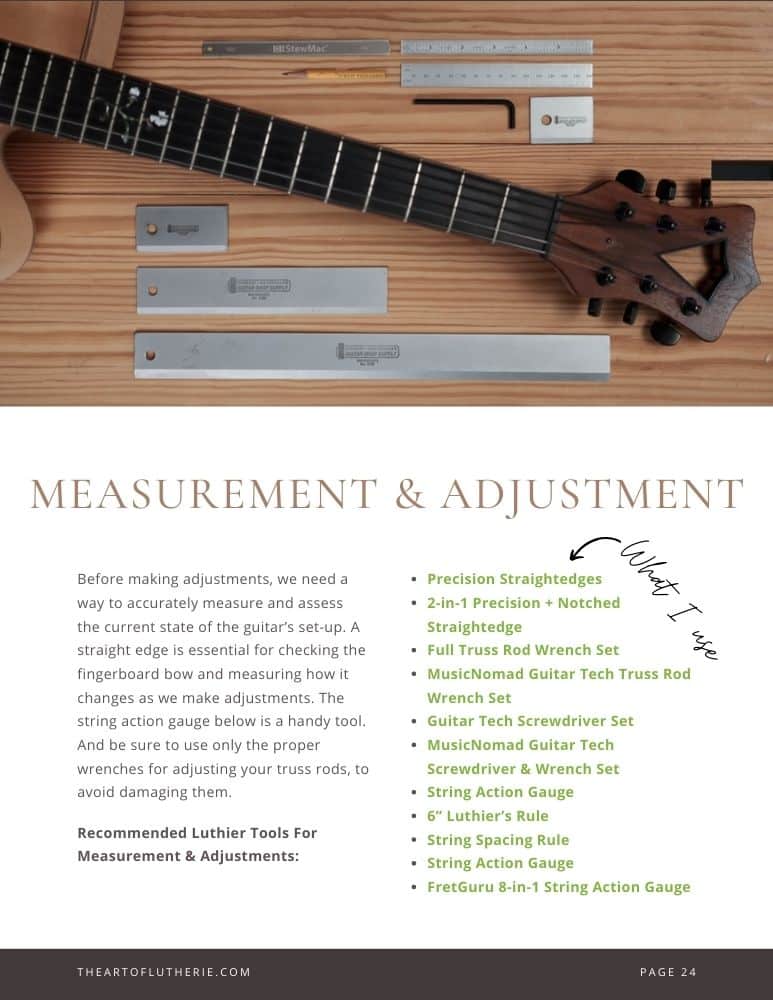
Credit: theartoflutherie.com
Finishing And Set-up Tools
Bringing a handmade electric guitar to life isn’t just about crafting its body and neck—it’s also about the crucial stages of finishing and set-up. This phase transforms a rudimentary construction into an instrument that looks professional and produces high-quality sound. The right tools not only make this process possible but can also elevate the quality of your guitar. Explore these essential tools for applying finishes, setting up the playability, and achieving the perfect aesthetic and sound every guitarist dreams of.
Spray Guns And Airbrushes: Applying Lacquer And Paint
A smooth, even finish on your electric guitar is paramount for visual appeal and protection of the wood. Spray guns are ideal for covering large surfaces with lacquer or paint, while airbrushes offer precision for detailed work and creating unique graphics. Both tools are crucial for applying layers of finish that can withstand the test of time and use.
Buffing And Polishing Equipment: Achieving A Glossy Finish
Once the paint and lacquer have dried, the next step is to attain that coveted glossy finish. Specialized buffing and polishing equipment removes imperfections and brings out a lustrous shine. This process involves varying grades of buffing compounds and polishing cloths to achieve a mirror-like finish that makes your guitar stand out.
Nut Files: Adjusting String Height
Proper string action is key to playability and comfort. Nut files are precision tools that enable you to finely adjust the height of each string at the nut, ensuring a comfortable action without fret buzz. Different gauges of nut files allow you to match the string width for a perfect fit, contributing to the overall tone and sustain of your instrument.
Truss Rod Wrench: Neck Adjustment
The neck of your guitar must have the correct curvature for optimal playability. A truss rod wrench fits your guitar’s truss rod nut and allows you to make precise adjustments to the neck’s relief. This tool is essential for combating issues such as warping, which can be caused by string tension and environmental changes.
String Winder And Cutter: String Installation And Tuning
The final setup of your electric guitar involves the painstaking task of installing and properly tuning the strings. A string winder speeds up the winding process, while a dedicated cutter trims the excess length, preventing unnecessary breakage and maintaining a tidy headstock. These tools simplify the string changing process and ensure that your guitar is always performance-ready.
Advanced Tools For Custom Guitar Features
Embarking on the journey of building a custom electric guitar involves not just passion and patience, but also the right set of tools. While basic hand tools can get you started, advanced equipment can elevate your craftsmanship, allowing you to add refined and complex features to your guitar. These high-tech tools bring a new level of precision and creativity to the guitar-making process, enabling both professional luthiers and ambitious DIYers to push the boundaries of their designs.
Cnc Machines: Precision Cutting For Complex Designs
Computer Numerical Control (CNC) machines are the cornerstone of modern guitar manufacturing, providing unparalleled accuracy in cutting body shapes, routing cavities, and carving neck profiles. A CNC machine, often guided by sophisticated software, can execute intricate patterns and deeply detailed work which would be incredibly time-consuming and difficult by hand.
3d Printers: Crafting Unique Hardware And Accessories
3D printing technology opens up a world of possibilities for creating custom hardware and guitar accessories. Fueled by CAD designs, a 3D printer can produce tailor-made tuning pegs, knobs, and even pickups. This allows for a high degree of personalization and the ability to prototype new guitar parts quickly and efficiently.
Laser Cutters: Intricate Inlay Work
For those who desire the beauty of detailed inlay work on their fretboards, headstocks or bodies, laser cutters are the go-to tool. These devices can etch and cut with exceptional precision, turning materials like wood, mother-of-pearl, or acrylic into stunning decorative pieces that are then inlaid into the guitar, enhancing its aesthetic and value.
Plek Machine: High-precision Fret Leveling
The Plek machine is a marvel of guitar tech, providing a means to achieve perfect action and playability. It uses advanced sensors to assess and automatically level and crown the frets to a high degree of accuracy, ensuring the guitar’s playability is second to none. The Plek process can also help in identifying issues with the neck and suggest the necessary adjustments to achieve optimal tension and intonation.
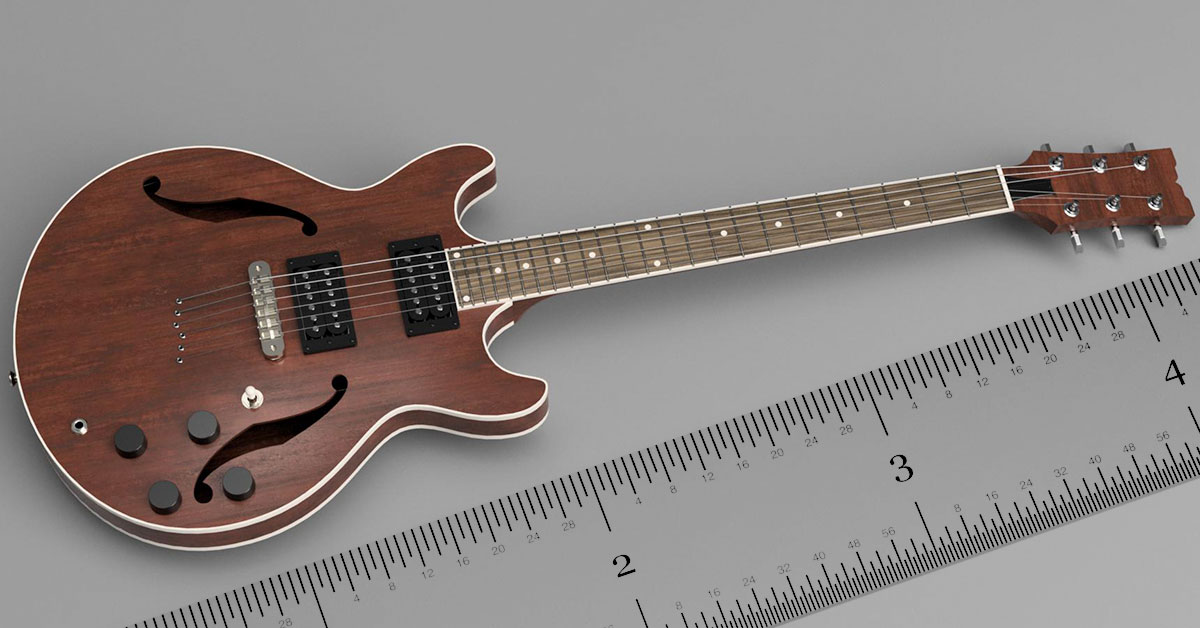
Credit: www.electricherald.com
Safety Precautions And Maintenance Of Tools
Building an electric guitar from scratch or performing modifications often involves the use of a variety of tools and machinery that can pose safety risks if not handled properly. It’s crucial to protect oneself and ensure that tools perform at their best over time by adopting rigorous safety protocols and maintenance routines. Let’s dive into the specifics of staying safe and keeping your tools in top condition.
Personal Protective Equipment: Ensuring Safety While Working
The creation of an electric guitar requires precision and attention to detail. As a luthier, one’s focus is not only on craftsmanship but also on personal safety. Personal Protective Equipment (PPE) is vital when working with potentially hazardous materials and tools. Here are essential PPE items to consider:
- Safety Glasses: Protect your eyes from wood shavings and dust.
- Ear Protection: Use earplugs or earmuffs when operating loud machinery.
- Respiratory Masks: A necessity to avoid inhaling dust and chemical fumes.
- Work Gloves: Shield your hands during rough work but remove them during precise tasks to maintain dexterity.
Proper Tool Storage And Care
Proper maintenance and storage of tools extend their lifespan and ensure they’re ready for use at any time. Tool care involves a few simple practices:
- Wipe metal parts with a light oil to prevent rust.
- Regularly sharpen cutting tools for efficiency and safety.
- Store tools in a dry environment to minimize moisture exposure.
- Validate electrical tools’ integrity by checking cords and plugs for damage.
Each tool has its own specific care routine which should be followed according to the manufacturer’s instructions for optimal performance.
Maintaining A Clean And Organized Workshop
An orderly workshop is essential for both safety and productivity. It’s easier to work efficiently when tools and materials are neatly arranged and readily available. Tool organization systems and labeled storage can greatly reduce the risk of accidents and time wasted searching for required items.
Regular cleanup sessions help to keep the workspace manageable. Key steps include:
- Disposing of scrap materials and waste.
- Cleaning up spills immediately to avoid slips.
- Ensuring walkways and emergency exits are clear of obstructions.
Maintaining an organized workshop is crucial for a smooth, uninterrupted guitar-making process and also contributes to the longevity of your tools.
Essential Supplies And Materials
Welcome to the world of custom electric guitar creation where the right tools and materials turn raw potential into stunning reality. Crafting an electric guitar requires not just skill and patience, but also a well-curated collection of essential supplies. From the soul-stirring vibrations of the strings to the finesse of the electronics that capture your unique sound, we’ll guide you through the vital components that you need to get started.
Guide To Selecting Guitar Strings And Materials
Choosing the correct strings is crucial for defining your guitar’s playability and tone. While strings may seem like a simple purchase, the material and gauge can make a dramatic difference.
- Nickel-plated strings offer a balanced and versatile sound, perfect for a range of genres.
- Stainless steel strings shine with brightness and sustain, suited for players wanting to cut through the mix.
- Pure nickel strings deliver a warm, vintage tone, reminiscent of classic rock and blues.
String gauge impacts playability; lighter gauges are easier on the fingers while heavier gauges provide more volume and sustain.
Pickups And Electronics: Customizing The Sound
An electric guitar’s voice is shaped by its pickups and electronics. The selection of these components is a pivotal step in achieving your desired sound.
Type | Description | Characteristics |
---|---|---|
Single-coil | Crisp and clear with a bright tone | Great for everything from blues to rock |
Humbucker | Rich and full with a warm tone | Ideal for jazz, rock, and metal |
P90 | A middle ground with a bit more edge | Perfect for achieving a vintage sound |
Besides pickups, electronic parts like potentiometers (volume and tone controls), switches (pickup selector), and output jacks are essential. Opt for high-quality components to ensure longevity and performance.
Frets, Bridges, And Tuners: Key Components For Playability
Accurate intonation, comfortable action, and stable tuning are all tied to the quality of your frets, bridges, and tuners.
- Frets: Nickel-silver alloys remain standard, but stainless steel offers longer wear.
- Bridges: Material choices include steel, brass, and graphite. Each affects sustain and tone differently.
- Tuners: Locking tuners stabilize tuning and simplify string changes. Ensure tuners are compatible with your headstock.
Remember that each choice reflects your personal playstyle and the unique sound you are chasing. Ensure components match your guitar’s design for seamless assembly and optimal performance.
Conclusion: Crafting Your Own Unique Electric Guitar
Embarking on the journey to create your own electric guitar is a testament to both creativity and technical skill. With the right set of tools and a deep well of patience, you can transform raw materials into a melodic masterpiece that is uniquely yours. As we wrap up our discussion on the essential tools for making an electric guitar, let’s reflect on the gratifying process, offer guidance for novices, and explore avenues for ongoing learning and community support.
The Rewarding Journey Of Guitar Building
Building an electric guitar from scratch is more than a DIY project—it’s an artistic endeavor that yields immense satisfaction. Each decision, from choosing the wood for the body to the intricacies of wiring, culminates in a one-of-a-kind instrument with personal significance. The blend of precision engineering and aesthetic flair required in this process cannot be understated.
Tips For First-time Guitar Makers
- Start simple: For your first build, choose a design that’s less complex to ensure a smoother learning curve.
- Quality materials: Invest in high-quality wood and components. Your efforts deserve the best raw materials.
- Precise measurements: Accuracy is crucial. Double-check measurements and alignments before cutting or drilling.
- Patience pays: Take your time at each stage. Rushing can lead to mistakes that are hard to correct.
Continuing Education And Community Resources For Luthiers
Once you’ve completed your first build, the learning shouldn’t stop there. Numerous resources are available for luthiers of all levels:
- Books and online tutorials can provide deeper insights into advanced techniques and styles.
- Workshops and classes at local community colleges or craft centers enhance skills under expert guidance.
- Forums and social media groups connect you with fellow guitar makers for tips, inspiration, and support.
With a commitment to ongoing education and connection with the luthier community, your skills and artistry will continue to grow, allowing you to tackle more ambitious projects and refine your craft.

Credit: projectelectricguitar.com
How Do the Parts of an Electric Guitar Relate to the Tools Needed to Make One?
Creating an electric guitar requires a deep understanding electric guitar components. From pickups to potentiometers, each part plays a crucial role in sound production. Tools like soldering irons and fret files are essential for assembly. Mastering these elements ensures a functional instrument that resonates with the player’s unique style.
Frequently Asked Questions On What Tools Do You Need To Make An Electric Guitar
What Tools Do You Need To Set Up An Electric Guitar?
To set up an electric guitar, you’ll need a tuner, string winder, wire cutter, screwdrivers, hex wrenches, and a cleaning cloth. Ensure you use the appropriate tools for your specific guitar model to avoid any damage.
What Materials Are Used To Make A Guitar?
Guitars are typically made from woods like spruce, maple, rosewood, and mahogany. Electric guitars also use metals and plastics for components such as pickups and knobs.
What Is Required For Electric Guitar?
An electric guitar requires an amplifier, a cable, guitar picks, a strap, and occasionally effects pedals. Regular maintenance, including new strings and setup adjustments, ensures optimal performance.
What Do I Need To Build A Guitar?
To build a guitar, you need wood for the body, neck, fretboard, and bracing. Tuning machines, strings, fret wire, glue, and finishing supplies are essential. Tools like saws, sanders, clamps, and a soldering iron for wiring are also necessary.
Conclusion
Crafting your own electric guitar can be immensely satisfying. With the right set of tools, this project is within your grasp. Remember to gather quality materials, invest in reliable equipment, and follow safety guidelines. Embrace the journey of building your musical masterpiece, and let the creativity flow.
Happy strumming!